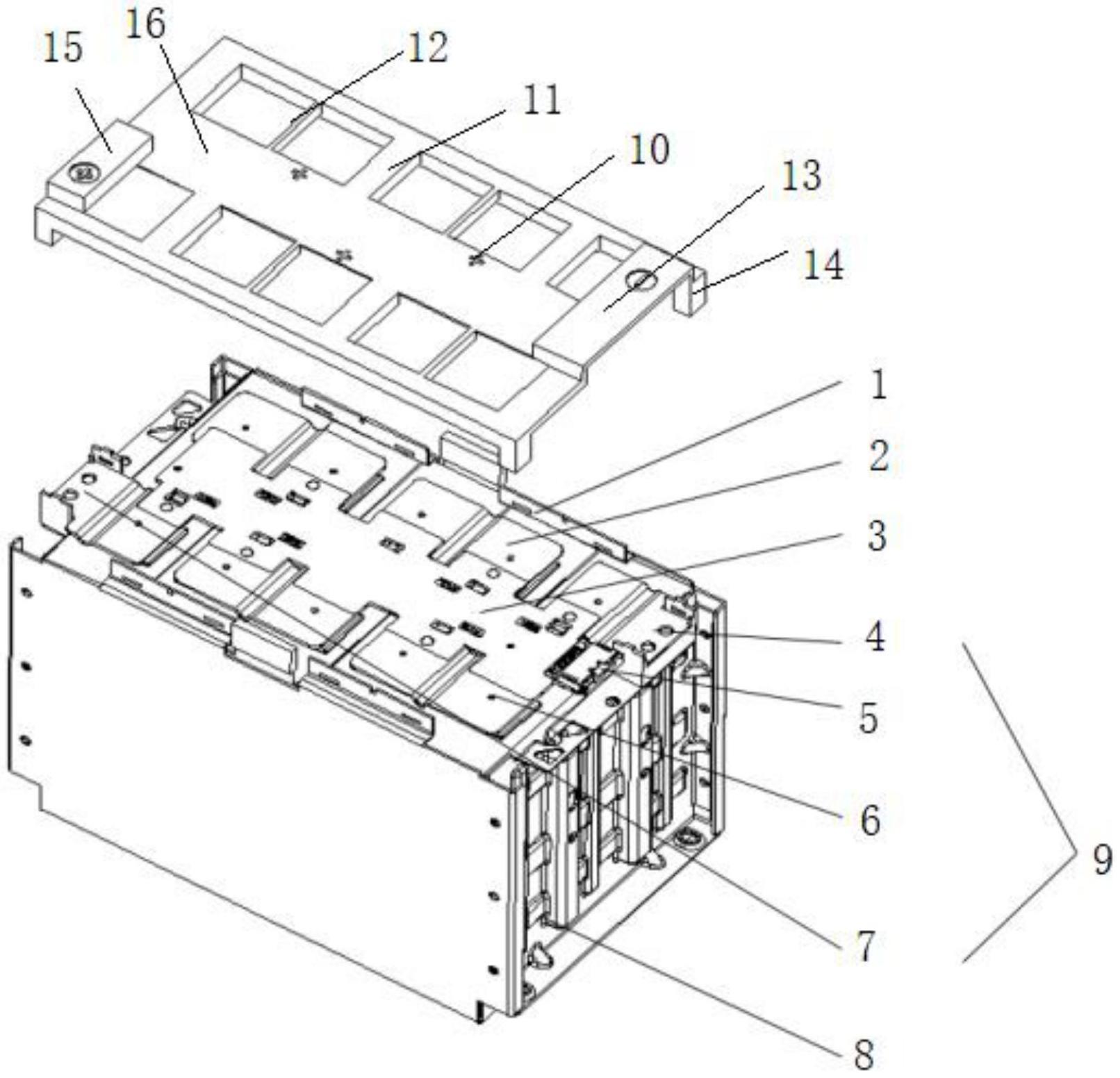
1.本实用新型涉及电池模组焊接技术领域,尤其涉及一种叉车锂电池模组焊接工装。
背景技术:2.目前在叉车锂电池模组的极片固定方面,考虑到控制产品的综合成本,将原先的有极片限位的集成盖板结构改成了无极片限位的pcb板结构,设计变更后会导致:
3.由于在焊接过程中,电芯本身存在高度差,致使pcb板上极片与电芯极柱无法充分贴合,必然会存在间隙,该间隙会导致虚焊,虚焊会导致严重的后果,如整车运行过程中的bms报警或整车无法运行;
4.pcb板整体与模组无限位设计,在焊接过程中pcb板一旦晃动就会导致模组焊接不良,严重时会导致激光击穿模组;
5.无防护的pcb板焊接不良率较高,增加生产和售后成本;
6.焊接压头下压长极片时,会导致长极片翘起,影响后续极片焊接,增加返工成本。
技术实现要素:7.本实用新型的目的是为了解决背景技术中指出的问题,而提出的一种叉车锂电池模组焊接工装。
8.为了实现上述目的,本实用新型采用了如下技术方案:
9.一种叉车锂电池模组焊接工装,电池模组包括外壳体,所述外壳体内叠放安装有若干个电芯,若干个所述电芯通过多个电芯串联极片串联连接,多个所述电芯串联极片之间安装有pcb板,所述焊接工装包括网压板,所述网压板与外壳体限位装配,所述网压板具有极片粗限位柱、极片细限位柱、pcb板下压部、焊接空间,所述极片细限位柱压设在电芯串联极片凹槽的位置,沿多个电芯叠放方向所述极片粗限位柱位于相邻两个电芯串联极片之间,所述电芯串联极片端部抵靠极片粗限位柱侧面,所述pcb板下压部压设在pcb板正上方。
10.所述外壳体沿多个电芯叠放方向的两端具有模组端板,所述模组端板四角具有插入间隙,所述网压板底面四角具有向下凸出的工装限位柱,所述工装限位柱限位在所述插入间隙内。
11.所述外壳体具有两个与模组端板垂直的模组侧板,所述模组侧板顶端具有向上凸出的侧板翻边,所述网压板限位在两个模组侧板的侧板翻边之间。
12.所述网压板顶面具有与电芯正极相匹配的正极标识。
13.所述电池模组具有与外界设备电连接的负极极片、正极极片,所述网压板正对负极极片的位置设有负极保护凸台,所述网压板正对正极极片的位置设有正极保护凸台。
14.所述电池模组设有信号端子,所述信号端子位于负极保护凸台正下方;
15.或者所述信号端子位于正极保护凸台正下方。
16.本实用新型提出的一种叉车锂电池模组焊接工装,有益效果在于:通过本工装有
效的避免焊接过程中的pcb板晃动,提升整体焊接质量,降低产品不良率,该模组焊接工装能够有效避免焊接过程中的长极片翘起的问题;该模组焊接工装操作简单,能够有效提高模组焊接速度和焊接合格率。
附图说明
17.图1为本实用新型的网压板结构示意图;
18.图2为本实用新型的网压板装配在电池模组上的结构示意图;
19.图3为本实用新型的网压板与电池模组分解结构示意图。
20.图中:侧板翻边1、电芯串联极片2、pcb板3、负极极片4、信号端子5、极片观察孔6、正极极片7、模组端板8、正负极片9、正极标识10、极片粗限位柱11、极片细限位柱12、负极保护凸台13、工装限位柱14、正极保护凸台15、pcb板下压部16。
具体实施方式
21.下面将结合本实用新型实施例中的附图,对本实用新型实施例中的技术方案进行清楚、完整地描述,显然,所描述的实施例仅仅是本实用新型一部分实施例,而不是全部的实施例。
22.参照图1-3,一种叉车锂电池模组焊接工装,电池模组包括外壳体,外壳体内叠放安装有若干个电芯,若干个电芯通过多个电芯串联极片2串联连接,多个电芯串联极片2之间安装有pcb板3,焊接工装包括网压板,网压板与外壳体限位装配,网压板具有极片粗限位柱11、极片细限位柱12、pcb板下压部16、焊接空间,极片细限位柱12压设在电芯串联极片2凹槽的位置,沿多个电芯叠放方向极片粗限位柱11位于相邻两个电芯串联极片2之间,电芯串联极片2端部抵靠极片粗限位柱11侧面,pcb板下压部16压设在pcb板3正上方。
23.使用时,将电芯串联极片2、pcb板3位置摆放好,然后将网压板与外壳体限位装配,通过pcb板下压部16压紧pcb板,通过极片细限位柱12压设在电芯串联极片2凹槽,使电芯串联极片2的位置固定,同时防止焊接过程中极片翘起,通过极片粗限位柱11的侧面对电芯串联极片2进行限位,防止焊接过程中的极片晃动。
24.通过本工装有效的避免焊接过程中的pcb板晃动,提升整体焊接质量,降低产品不良率,该模组焊接工装能够有效避免焊接过程中的长极片翘起的问题;该模组焊接工装操作简单,能够有效提高模组焊接速度和焊接合格率。
25.作为一种实施方式,在每个极片位于电芯极性的位置均开设一个极片观察孔6,焊接工装固定后通过极片观察孔观察电芯极性与正负极标识是否一致,不一致时及时进行返工,该模组焊接工装增加极性检测功能,能够检查模组极性。
26.作为网压板与外壳体限位装配的一种实施方式,外壳体沿多个电芯叠放方向的两端具有模组端板8,模组端板8四角具有插入间隙,网压板底面四角具有向下凸出的工装限位柱14,工装限位柱14限位在插入间隙内,利用外壳体的插入间隙与网压板的工装限位柱14配合的方式实现限位装配作用。
27.进一步的,外壳体具有两个与模组端板8垂直的模组侧板,模组侧板顶端具有向上凸出的侧板翻边1,网压板限位在两个模组侧板的侧板翻边1之间,通过侧板翻边1对网压板进行二次限位,防止工装在宽度方向上发生晃动。
28.为了方便观察电池模组极性标识,网压板顶面具有与电芯正极相匹配的正极标识10。
29.作为一种实施方式,电池模组具有与外界设备电连接的负极极片4、正极极片7,网压板正对负极极片4的位置设有负极保护凸台13,网压板正对正极极片7的位置设有正极保护凸台15;电池模组设有信号端子5,信号端子5位于负极保护凸台13正下方;或者信号端子5位于正极保护凸台15正下方。通过该种设置,焊接过程中避免压头损坏负极极片4、正极极片7、信号端子。
30.以上所述,仅为本实用新型较佳的具体实施方式,但本实用新型的保护范围并不局限于此,任何熟悉本技术领域的技术人员在本实用新型揭露的技术范围内,根据本实用新型的技术方案及其实用新型构思加以等同替换或改变而得到的技术方案、构思、设计,都应涵盖在本实用新型的保护范围之内。
技术特征:1.一种叉车锂电池模组焊接工装,电池模组包括外壳体,所述外壳体内叠放安装有若干个电芯,若干个所述电芯通过多个电芯串联极片(2)串联连接,多个所述电芯串联极片(2)之间安装有pcb板(3),其特征在于,所述焊接工装包括网压板,所述网压板与外壳体限位装配,所述网压板具有极片粗限位柱(11)、极片细限位柱(12)、pcb板下压部(16)、焊接空间,所述极片细限位柱(12)压设在电芯串联极片(2)凹槽的位置,沿多个电芯叠放方向所述极片粗限位柱(11)位于相邻两个电芯串联极片(2)之间,所述电芯串联极片(2)端部抵靠极片粗限位柱(11)侧面,所述pcb板下压部(16)压设在pcb板(3)正上方。2.根据权利要求1所述的一种叉车锂电池模组焊接工装,其特征在于,所述外壳体沿多个电芯叠放方向的两端具有模组端板(8),所述模组端板(8)四角具有插入间隙,所述网压板底面四角具有向下凸出的工装限位柱(14),所述工装限位柱(14)限位在所述插入间隙内。3.根据权利要求2所述的一种叉车锂电池模组焊接工装,其特征在于,所述外壳体具有两个与模组端板(8)垂直的模组侧板,所述模组侧板顶端具有向上凸出的侧板翻边(1),所述网压板限位在两个模组侧板的侧板翻边(1)之间。4.根据权利要求1所述的一种叉车锂电池模组焊接工装,其特征在于,所述网压板顶面具有与电芯正极相匹配的正极标识(10)。5.根据权利要求1所述的一种叉车锂电池模组焊接工装,其特征在于,所述电池模组具有与外界设备电连接的负极极片(4)、正极极片(7),所述网压板正对负极极片(4)的位置设有负极保护凸台(13),所述网压板正对正极极片(7)的位置设有正极保护凸台(15)。6.根据权利要求5所述的一种叉车锂电池模组焊接工装,其特征在于,所述电池模组设有信号端子(5),所述信号端子(5)位于负极保护凸台(13)正下方;或者所述信号端子(5)位于正极保护凸台(15)正下方。
技术总结本实用新型涉及电池模组焊接技术领域,尤其是一种叉车锂电池模组焊接工装,包括网压板,所述网压板与外壳体限位装配,所述网压板具有极片粗限位柱、极片细限位柱、pcb板下压部、焊接空间,所述极片细限位柱压设在电芯串联极片凹槽的位置,沿多个电芯叠放方向所述极片粗限位柱位于相邻两个电芯串联极片之间,所述电芯串联极片端部抵靠极片粗限位柱侧面,所述pcb板下压部压设在pcb板正上方。通过本工装有效的避免焊接过程中的pcb板晃动,提升整体焊接质量,降低产品不良率,该模组焊接工装能够有效避免焊接过程中的长极片翘起的问题;该模组焊接工装操作简单,能够有效提高模组焊接速度和焊接合格率。速度和焊接合格率。速度和焊接合格率。
技术研发人员:孙仁诣 叶小凌 张书维
受保护的技术使用者:安徽和鼎机电设备有限公司
技术研发日:2023.04.23
技术公布日:2023/10/27