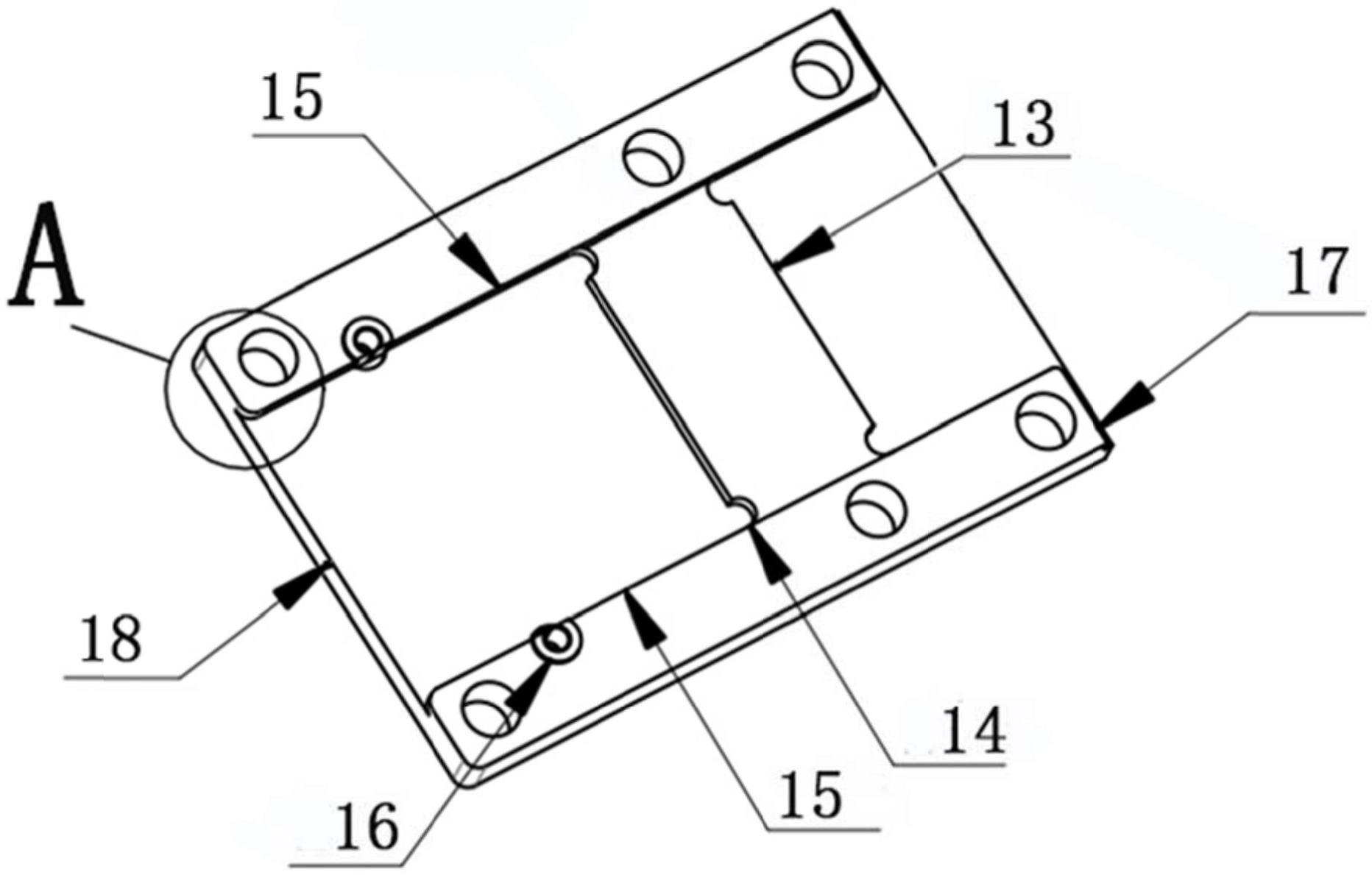
1.本实用新型属于机械技术领域,特别涉及一种破碎锤夹板。
背景技术:2.液压破碎锤作为液压挖掘机的一个重要的作业属具,不断在各个领域得到广泛应用,矿山开采、冶金、公路、铁路、建筑等行业都能见到其忙碌身影。日益恶劣的应用环境,加上高频的打击、破碎、振动等对破碎锤自身的设计、制造带来了一定的考验,其中破碎锤夹板在使用过程中就经常遇到开裂问题,而且扁销挡销作为易损件,在工地中频繁的进行拆装,对破碎锤夹板带来了一定的磨损,严重影响到夹板的使用寿命。
技术实现要素:3.本实用新型提出了一种破碎锤夹板,能够有效的解决破碎锤工作打击、振动过程中破碎锤夹板本体易开裂的问题,同时降低扁销和挡销拆装过程中对破碎锤夹板本体的磨损,从而提高破碎锤夹板本体的稳定性和使用寿命。
4.为实现上述目的,本发明采用如下技术方案:
5.一种破碎锤夹板,包括破碎锤夹板本体1,所述破碎锤夹板本体1内壁相对的两边设置有沉台15,两边沉台15与破碎锤夹板本体1内壁形成凹槽18,破碎锤前缸体3四周四个侧壁,其中一组相对的两个侧壁外各设置有一块破碎锤夹板本体1,所述破碎锤前缸体3的侧壁卡入破碎锤夹板本体1的凹槽18内;另一组相对的两个侧壁外各设置一个挡销4,挡销4的两端分别插入相对的两块破碎锤夹板本体1中,两块破碎锤夹板本体1和两个挡销4将破碎锤前缸体3四周进行围挡,位于破碎锤前缸体3内,沿着两个挡销4相对的方向贯穿有扁销5。
6.进一步的,所述破碎锤夹板本体1上位于破碎锤前缸体3外边缘处设置有挡销孔16,所述挡销孔16内安装有挡销堵套2,所述挡销4插入挡销堵套2内。
7.进一步的,所述沉台15的两边均设置有圆弧角11。
8.进一步的,所述沉台15与破碎锤前缸体3相接触的边为圆角边12。
9.进一步的,所述破碎锤夹板本体1内壁上两边沉台15之间设置有凸台13,所述凸台13与破碎锤前缸体3外壁上的凹槽相匹配。
10.进一步的,所述凸台13与两边沉台15相接的角落设置有角部圆弧14。
11.进一步的,所述凸台13的高度低于凹槽18的深度。
12.进一步的,所述破碎锤前缸体3的前端连接有钎杆8,所述破碎锤前缸体3的尾部连接有破碎锤中缸体7。
13.进一步的,所述破碎锤夹板本体1的尾部设置有尾部沉台17,尾部沉台17与破碎锤中缸体紧密贴合。
14.进一步的,所述破碎锤中缸体7相对的两个侧壁上各设置有一个破碎锤夹块6。
15.与现有技术相比,本实用新型具有以下有益效果:
16.本实用新型有效降低破碎锤在工作中对破碎锤夹板本体的冲击、振动而导致开裂的风险,大大提高破破碎锤夹板本体的使用寿命,拆装简便,从而有效减少破碎锤夹板本体装配及售后维修人员的劳动强度。
附图说明
17.图1是本实用新型的结构示意图;
18.图2是本实用新型的剖面图;
19.图3是本实用新型中破碎锤夹板本体的结构示意图;
20.图4是图3中a的结构示意图;
21.图中:1-破碎锤夹板本体、11-圆弧角、12-圆角边、13-凸台、14-角部圆弧、15-沉台、16-挡销孔、17-尾部沉台、18-凹槽、2-挡销堵套、3-破碎锤前缸体、4-挡销、5-扁销、6-破碎锤夹块、7-破碎锤中缸体、8-钎杆。
具体实施方式
22.下面结合附图对本发明做更进一步的解释。
23.如图1-4所示,一种破碎锤夹板,包括破碎锤夹板本体1,所述破碎锤夹板本体1内壁相对的两边设置有沉台15,两边沉台15与破碎锤夹板本体1内壁形成凹槽18,破碎锤前缸体3四周四个侧壁,其中一组相对的两个侧壁外各设置有一块破碎锤夹板本体1,所述破碎锤前缸体3的侧壁卡入破碎锤夹板本体1的凹槽18内;另一组相对的两个侧壁外各设置一个挡销4,挡销4的两端分别插入相对的两块破碎锤夹板本体1中,两块破碎锤夹板本体1和两个挡销4将破碎锤前缸体3四周进行围挡,位于破碎锤前缸体3内,沿着两个挡销4相对的方向贯穿有扁销5。因为破碎锤在工作中,存在一些摇晃钎杆、外力撞击、螺栓松动、磨损等客观因素,使得破碎锤夹板本体1与破碎锤前缸体3配合区域受到一定的冲击,尤其是破碎锤夹板本体1与破碎锤前缸体3相接的圆弧角11和沉台15边的沟槽部位往往很容易会产生疲劳裂纹;沉台15和凹槽18,在破碎锤夹板本体1上与破碎锤前缸体3贴合的位置增设沉台15,沉台15与破碎锤夹板本体1内壁形成的凹槽18包裹破碎锤前缸体3的三个外壁,有效地增加破碎锤夹板本体1与破碎锤前缸体3之间的接触面积,保证破碎锤夹板本体1三个槽面与破碎锤前缸体3三个侧壁紧密的贴合,提高结构的稳定性。
24.作为一个优选方案,所述破碎锤夹板本体1上位于破碎锤前缸体3外边缘处设置有挡销孔16,所述挡销孔16内安装有挡销堵套2,所述挡销4插入挡销堵套2内;破碎锤的挡销4在工作中频繁拆装,对挡销孔16磨损较为严重,同时现有技术中市面上挡销完全装配在破碎锤前缸体内部,在破碎锤打击过程中,因破碎锤前缸体最靠近被破碎对象,极易受到载荷冲击、外物撞击等问题,而且由于一些挖机机手不良操作(破碎锤频繁空打),也会导致破碎锤前缸体的撕裂等问题产生,现有技术中,挡销孔在破碎锤夹板本体上的位置,相对于破碎锤前缸体位于其内部,本实用新型将挡销孔16移至破碎锤前缸体3外部,具体的讲,所述破碎锤夹板本体1上位于破碎锤前缸体3外边缘处设置有挡销孔16,即破碎锤前缸体3上不需要额外加工挡销孔16,有效地将开孔位置避开了破碎锤前缸体3高应力区域,避免了因孔间(扁销孔、扁销挡销孔)相互影响而造成应力集中系数增高,从而减少破碎锤前缸体3撕裂问题,同时挡销4在破碎锤前缸体3外部进行装配,可以有效降低装配难度,提高维修人员工作
效率。挡销堵套2,在挡销孔16上通过冷装工艺方式,装配挡销堵套2,挡销堵套2通过热处理工艺,具有高耐磨性能,装配后大大提升了破碎锤夹板本体1的耐磨性能,从而延长夹板的使用寿命。
25.作为一个优选方案,所述沉台15的两边均设置有圆弧角11,因为破碎锤在工作中,存在一些摇晃钎杆、外力撞击、螺栓松动、磨损等客观因素,使得破碎锤夹板本体1与破碎锤前缸体3配合区域受到一定的冲击,尤其是破碎锤夹板本体1与破碎锤前缸体3相接的圆弧角11和沉台15边的沟槽部位往往很容易会产生疲劳裂纹,圆弧角11,位于破碎锤夹板本体1上沉台15的两端位置,现有技术中为尖角设计,本实用新型中将尖角改为圆弧角11,有效地降低了冲撞、震动时对于破碎锤夹板本体1的损害程度。
26.作为一个优选方案,所述沉台15与破碎锤前缸体3相接触的边为圆角边12,因为破碎锤在工作中,存在一些摇晃钎杆、外力撞击、螺栓松动、磨损等客观因素,使得破碎锤夹板本体1与破碎锤前缸体3配合区域受到一定的冲击,尤其是破碎锤夹板本体1与破碎锤前缸体3相接的圆弧角11和沉台15边的沟槽部位往往很容易会产生疲劳裂纹,圆角边12,位于破碎锤夹板本体1上沉台15与破碎锤前缸体3相接的边,取消现有技术在加工过程中的清角操作,保留加工中刀具圆角,不仅可以降低破碎锤夹板本体1与破碎锤前缸体3之间冲撞与震动的力道,同时也可以减少加工工序,提高生产效率。
27.作为一个优选方案,所述破碎锤夹板本体1内壁上两边沉台15之间设置有凸台13,所述凸台13与破碎锤前缸体3外壁上的凹槽相匹配,所述凸台13与两边沉台15相接的角落设置有角部圆弧14,所述凸台13的高度低于凹槽18的深度;因为破碎锤在工作中,存在一些摇晃钎杆、外力撞击、螺栓松动、磨损等客观因素,使得破碎锤夹板本体1与破碎锤前缸体3配合区域受到一定的冲击,尤其是破碎锤夹板本体1与破碎锤前缸体3相接的圆弧角11和沉台15边的沟槽部位往往很容易会产生疲劳裂纹,本实用新型通过以下三个部分有效地避免此问题的产生:角部圆弧14,位于凸台13与两边沉台15相接的角落设置有角部圆弧14,使得凸台13与破碎锤前缸体3之间更加契合。
28.作为一个优选方案,所述破碎锤前缸体3的前端连接有钎杆8,所述破碎锤前缸体3的尾部连接有破碎锤中缸体7,所述破碎锤夹板本体1的尾部设置有尾部沉台17,尾部沉台17与破碎锤中缸体紧密贴合;破碎锤在高频振动打击过程中,破碎锤夹板本体1很容易产生松动问题,并带来磨损、疲劳裂纹等一系列问题,尾部沉台17,破碎锤夹板本体1尾部增设尾部沉台17,尾部沉台17与破碎锤中缸体紧密贴合,起到支撑保护作用,破碎锤在钎杆上下打击过程中,可有效的减少打击方向的松动问题。
29.作为一个优选方案,所述破碎锤中缸体7相对的两个侧壁上各设置有一个破碎锤夹块6,两个破碎锤夹块6之间通过螺栓、螺母、垫片等连接固定(此部分未画图),两个破碎锤夹块6与两块破碎锤夹板本体1的位置相匹配。
30.本实用新型的原理:
31.一、因为破碎锤在工作中,存在一些摇晃钎杆、外力撞击、螺栓松动、磨损等客观因素,使得破碎锤夹板本体1与破碎锤前缸体3配合区域受到一定的冲击,尤其是破碎锤夹板本体1与破碎锤前缸体3相接的圆弧角11和沉台15边的沟槽部位往往很容易会产生疲劳裂纹,本实用新型通过以下三个部分有效地避免此问题的产生:
32.(1)圆弧角11,位于破碎锤夹板本体1上沉台15的两端位置,现有技术中为尖角涉
及,本实用新型中将尖角改为圆弧角11,有效地降低了冲撞、震动时对于破碎锤夹板本体1的损害程度;
33.(2)圆角边12,位于破碎锤夹板本体1上沉台15与破碎锤前缸体3相接的边,取消现有技术在加工过程中的清角操作,保留加工中刀具圆角,不仅可以降低破碎锤夹板本体1与破碎锤前缸体3之间冲撞与震动的力道,同时也可以减少加工工序,提高生产效率;
34.(3)角部圆弧14,位于凸台13与两边沉台15相接的角落设置有角部圆弧14,使得凸台13与破碎锤前缸体3之间更加契合;
35.二、破碎锤在高频振动打击过程中,破碎锤夹板本体1很容易产生松动问题,并带来磨损、疲劳裂纹等一系列问题,本实用新型通过以下两个部分有效地规避了此问题产生:
36.(1)沉台15和凹槽18,在破碎锤夹板本体1上与破碎锤前缸体3贴合的位置增设沉台15,沉台15与破碎锤夹板本体1内壁形成的凹槽18包裹破碎锤前缸体3的三个外壁,有效地增加破碎锤夹板本体1与破碎锤前缸体3之间的接触面积,保证破碎锤夹板本体1三个槽面与破碎锤前缸体3三个侧壁紧密的贴合,提高结构的稳定性;
37.(2)尾部沉台17,破碎锤夹板本体1尾部增设尾部沉台17,尾部沉台17与破碎锤中缸体紧密贴合,起到支撑保护作用,破碎锤在钎杆上下打击过程中,可有效的减少打击方向的松动问题;
38.三、破碎锤的挡销4在工作中频繁拆装,对挡销孔16磨损较为严重,同时现有技术中市面上挡销完全装配在破碎锤前缸体内部,在破碎锤打击过程中,因破碎锤前缸体最靠近被破碎对象,极易受到载荷冲击、外物撞击等问题,而且由于一些挖机机手不良操作(破碎锤频繁空打),也会导致破碎锤前缸体的撕裂等问题产生,本实用新型通过以下两个部分可以有效地解决上述问题:
39.(1)挡销孔16,现有技术中,挡销孔在破碎锤夹板本体上的位置,相对于破碎锤前缸体位于其内部,本实用新型将挡销孔16移至破碎锤前缸体3外部,具体的讲,所述破碎锤夹板本体1上位于破碎锤前缸体3外边缘处设置有挡销孔16,即破碎锤前缸体3上不需要额外加工挡销孔16,有效地将开孔位置避开了破碎锤前缸体3高应力区域,避免了因孔间(扁销孔、扁销挡销孔)相互影响而造成应力集中系数增高,从而减少破碎锤前缸体3撕裂问题,同时挡销4在破碎锤前缸体3外部进行装配,可以有效降低装配难度,提高维修人员工作效率。
40.(2)挡销堵套2,在挡销孔16上通过冷装工艺方式,装配挡销堵套2,挡销堵套2通过热处理工艺,具有高耐磨性能,装配后大大提升了破碎锤夹板本体1的耐磨性能,从而延长夹板的使用寿命。
41.以上所述仅是本发明的优选实施方式,应当指出,对于本技术领域的普通技术人员来说,在不脱离本发明原理的前提下,还可以做出若干改进和润饰,这些改进和润饰也应视为本发明的保护范围。