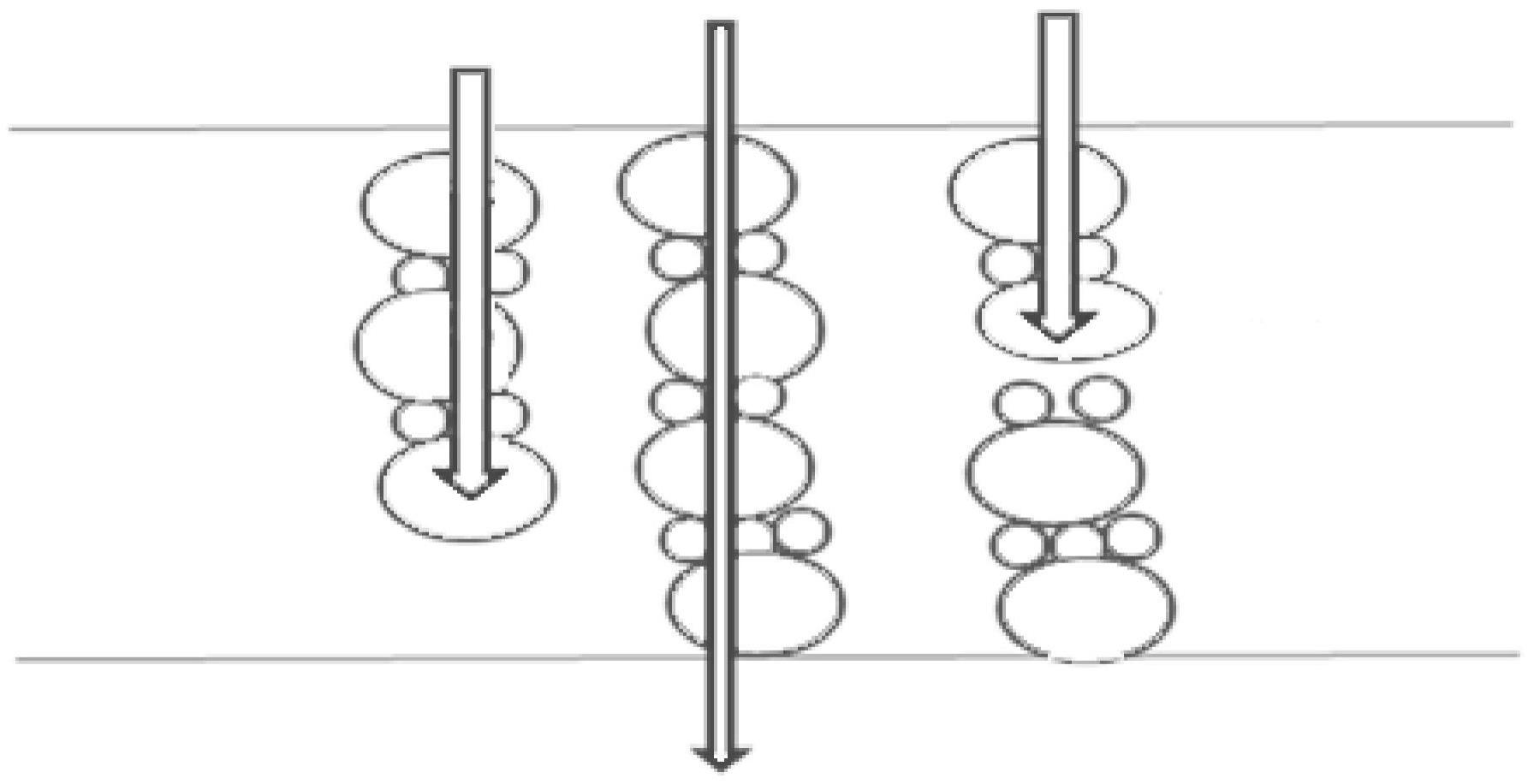
1.本发明涉及铜铝复合板领域,具体而言,涉及一种新型的铜铝复合板及制备方法。
背景技术:2.随着金属基线路板的发展,电源板、大功率照明以及汽车板的应用越来越广泛,对于基底材料的散热性能提出越来越高的要求。在工作时,由于固定的小空间范围内会产生大量的热量,该热量无法通过常规方式自行散发,因此会影响到基底材料上灯珠的寿命。
3.目前,行业内通常采用的散热方式是在灯珠等器件封装的背部加上金属凸台作为导体,将热量迅速的散发掉,该工艺中的金属凸台导体通常为铜。但目前用铜基板制作金属凸台存在有重量大、价格高、生产流程长、工艺复杂,对设备制程能力要求高,无法精确在铜基板上蚀刻出凸台的缺点。
4.铜铝复合板是一种以铝为基体,铜为覆层的双金属复合材料,相比于单一介质的金属板,铜铝复合板具有非常好的散热功能和可加工性,可以实现轻量化,在保持结构性能的前提下,大大减少板材的重量。铜铝复合板还具有非常好的加工性,可以符合各种尺寸和设计的要求,如进行折弯、冲压、焊接等加工设计不同的形状和尺寸。此外,因使用铝作为基底,相对于铜基板具有很大的成本优势。而目前市面上的铜铝复合板多是通过冷轧、热轧、爆炸复合法、爆炸轧制法等方式焊接在一起,存在有散热性较差、结合力不高的问题。
5.有鉴于此,特提出本发明。
技术实现要素:6.本发明的第一目的在于提供一种用于铜铝复合板的粘接组合物,该粘接组合物包括有双酚a型酚醛环氧树脂和导热导电粉体,导热导电粉体能够在树脂内通过粒径不同的粉体进行复配组合,形成良好的导热通道和导电路径,从而提高铜铝复合板的散热性能,确保铜铝复合板的具有良好的导电性;以双酚a型酚醛环氧树脂为原材料的粘接组合物,对金属的黏着力很强,力学强度高,足够满足铜铝复合板对于结合力的需求。
7.为实现本发明的上述目的,特采用一下技术方案:
8.本发明提供了一种用于铜铝复合板的粘接组合物,包括有双酚a型酚醛环氧树脂和导热导电粉体,按质量份数计,包括所述双酚a型酚醛环氧树脂25-30份,所述导热导电粉体70-75份。
9.由于粉体的粒径越小,相同重量的比表面积就越大,也就需要更多环氧树脂去包覆,粉体过少会降低散热性能,而环氧树脂过少则会降低结合力。因此需要特定将环氧树脂和导热导电粉体的质量比限定为(2.5-3.0):(7.0-7.5),才能实现散热性能和结合力的兼顾。
10.优选的,所述导热导电粉体包括,按质量份数计,铜粉15-22份,铝粉10-20份,炭黑粉体20-40份,角型氧化铝0-10份。
11.由铜粉、铝粉、炭黑粉末和角型氧化铝组成的导热导电粉体能够形成良好的导热
通道,从而实现产品散热性能的提高。其中,铜粉和铝粉的密度较大,与树脂混合后极易出现沉降的情况,从而导致无法形成良好的导热通道,因此需要铜粉、铝粉的质量分别不超过导热导电粉体的30%,以保证铜铝复合板的散热性能。
12.优选的,所述铜粉的粒径为3-5um,所述铝粉的粒径为2-3um,所述炭黑粉体的粒径为1-3um,所述角型氧化铝的粒径为1-2um。
13.除了粉体的选择,良好的导热通道需要通过大小不同的粒径进行合理的复配才能形成,因此各粉体选取的的粒径大小也会对产品的导热系数和结合力会产生影响。
14.优选的,按质量份数计,包括双酚a型酚醛环氧树脂30份,导热导电粉体70份;
15.导热导电粉体包括,以质量份数计:粒径为5um的铜粉15份,粒径为3um的铜粉5份,粒径为3um的铝粉12份,粒径为2um的铝粉8份,粒径为1um的炭黑粉体20份,粒径为1um的角型氧化铝10份。
16.作为本发明最佳的原料配比方案,该原料配比中双酚a型酚醛环氧树脂与导热导电粉体的质量比为3:7,在该质量比下导热导电粉体能够被环氧树脂充分包覆,产品的结合力效果更好;此外,通过大量的试验和结果分析,上述选取的粉体粒径、该粒径下的含量以及各粉体之间的用量配比关系所产生的协同作用最佳,从而使得产品最终能兼顾导热系数和结合力,使两者都能达到最佳效果。
17.优选的,还包括有固化剂和引发剂;
18.优选的,所述固化剂为双氰胺,所述引发剂为甲基咪唑,所述双酚a型酚醛环氧树脂的分子量为200-300g/eq,25℃时粘度为8000~11000cps。
19.使用低分子量的双酚a型酚醛环氧树脂,并以双氰胺作为固化剂,甲基咪唑作为引发剂,能够使粘接组合物具有结合力大,韧性强的特点,并且在制备时反应速度快。
20.本发明的第二目的在于提供一种粘接组合物的制备方法,包括以下步骤:
21.将双酚a型酚醛环氧树脂与导热导电粉体混合得到粘接膏体,将所述粘接膏体涂覆在铜板上,涂覆完成后烘烤使所述粘接膏体凝固,烘烤温度为70-90℃,烘烤时间为2-4分钟。
22.优选的,所述粘接膏体的涂覆厚度为8-12um,涂覆采用丝网印刷方式。
23.粘接膏体的涂覆厚度需要限定在一定参数内,厚度太小会导致通铝板出现接触不紧密充分的情况,厚度太大又会影响后续加工的结合力,容易出现铜铝板接触面分层的情况。此外,由于粘接膏体的厚度与铜、铝板相比较薄,因此通过丝网印刷方式,更易形成混匀厚度的粘结层。
24.本发明的第三目的在于提供一种使用上述制备方法得到的粘结组合物制备的铜铝复合板。
25.本发明还提供了铜铝复合板的制备方法,包括以下步骤:
26.将铝板与有粘接膏体一面的铜板对齐、压合,压合过程中进行抽真空和升温处理,真空度为50mmhg,压合完成后降温。
27.优选的,所述压合时升温速度为4-5℃/min,最高温段为170-200℃,最高温段持续时间为30-60min,降温速率为4-5℃/min;所述压合时的压力为10-20kg/cm2,压合时间为25-45min,升压时间为5-7min。
28.通过高温固化以及压合作用使粘接组合物与铜铝板接合,压合完成后放置进行缓
慢降温,以防止降温过快引起材料翘曲;在高温压合过程抽真空,能够防止粘结层产生气泡,以及高温下氧化情况的发生,同时还能降低压机的热损。
29.另一方面,高温压合的条件参数也会对产品的结合力和厚度均匀性产生影响,如本方案选用的固化温度为170-200℃,经试验确认在本发明的树脂体系下,过高的反应温度和过长反应时间均会引起树脂与粉体的分解,因此需要将参数控制在合理的范围内才能达到最佳的效果。
30.与现有技术相比,本发明的有益效果在于:
31.(1)本发明的粘接组合物通过环氧树脂以及导热导电粉体的相互配合,能够在树脂内形成导热通道以及导电路径,提高了铜铝复合板的散热性能和导电性能,同时还具有优秀的结合力和韧性强度。
32.(2)本发明公开了该反应体系下各参数的最佳配比以及选取范围,以及粘接组合物和应用粘接组合物的铜铝复合板的制备方法,制备方法高效稳定,铜铝复合板兼顾导热性能和结合力,生产工艺复杂度降低。
附图说明
33.通过阅读下文优选实施方式的详细描述,各种其他的优点和益处对于本领域普通技术人员将变得清楚明了。附图仅用于示出优选实施方式的目的,而并不认为是对本发明的限制。而且在整个附图中,用相同的参考符号表示相同的部件。在附图中:
34.图1为本发明所提供的形成导热通道和导电路径的示意图。
具体实施方式
35.下面将结合实施例对本发明的实施方案进行详细描述,但是本领域技术人员将会理解,下列实施例仅用于说明本发明,而不应视为限制本发明的范围。实施例中未注明具体条件者,按照常规条件或制造商建议的条件进行。所用试剂或仪器未注明生产厂商者,均为可以通过市售购买获得的常规产品。
36.实施例1
37.本实施例提供了一种用于铜铝复合板的粘接组合物,包括有双酚a型酚醛环氧树脂、导热导电粉体、双氰胺固化剂和甲基咪唑引发剂,其中,双酚a型酚醛环氧树脂28g,导热导电粉体70g。
38.其中,导热导电粉体包括:粒径为5um的铜粉20g,粒径为3um的铝粉10g,粒径为1um的炭黑粉体10g,粒径为3um的炭黑粉体30g。
39.其中,双酚a型酚醛环氧树脂的分子量为200-300g/eq,25℃时粘度为8000~11000cps,双氰胺固化剂和甲基咪唑引发剂的添加量为1.5g与0.05g。
40.将上述物质混合得到粘接膏体,采用丝网印刷方式将粘接膏体涂覆于铜板上,涂覆厚度为8um,涂覆完成后在70℃的条件下烘烤4分钟。
41.将铝板与有粘接膏体一面的铜板对齐,并在高温和真空度为50mmhg的条件下进行压合。其中,压合时升温速度为5℃/min,最高温段为200℃,最高温段持续时间为60min,压合时的压力为10kg/cm2,压合时间为45min,升压时间为5min。压合完成后缓慢降温,降温速度为5℃/min。
42.降温完成后得到产品铜铝复合板。
43.实施例2
44.本实施例提供了一种用于铜铝复合板的粘接组合物,包括有双酚a型酚醛环氧树脂、导热导电粉体、双氰胺固化剂和甲基咪唑引发剂,其中,双酚a型酚醛环氧树脂25g,导热导电粉体75g。
45.其中,导热导电粉体包括:粒径为5um的铜粉15g,粒径为3um的铜粉7g,粒径为2um的铝粉10g,粒径为1um的炭黑粉体13g,粒径为3um的炭黑粉体20g,粒径为2um的角型氧化铝10g。
46.其中,双酚a型酚醛环氧树脂的分子量为200-300g/eq,25℃时粘度为8000~11000cps,双氰胺固化剂和甲基咪唑引发剂的添加量为1.5g与0.05g。
47.将上述物质混合得到粘接膏体,采用丝网印刷方式将粘接膏体涂覆于铜板上,涂覆厚度为12um,涂覆完成后在90℃的条件下烘烤2分钟。
48.将将铝板与有粘接膏体一面的铜板对齐,并在高温和真空度为50mmhg的条件下进行压合。其中,压合时升温速度为5℃/min,最高温段为180℃,最高温段持续时间为50min,压合时的压力为20kg/cm2,压合时间为25min,升压时间为6min。压合完成后缓慢降温,降温速度为4℃/min。
49.降温完成后得到产品铜铝复合板。
50.实施例3
51.本实施例提供了一种用于铜铝复合板的粘接组合物,包括有双酚a型酚醛环氧树脂、导热导电粉体、双氰胺固化剂和甲基咪唑引发剂,其中,双酚a型酚醛环氧树脂30g,导热导电粉体70g。
52.其中,导热导电粉体包括:粒径为5um的铜粉15g,粒径为3um的铜粉5g,粒径为3um的铝粉12g,粒径为2um的铝粉8g,粒径为1um的炭黑粉体20g,粒径为1um的角型氧化铝10g。
53.其中,双酚a型酚醛环氧树脂的分子量为200-300g/eq,25℃时粘度为8000~11000cps,双氰胺固化剂和甲基咪唑引发剂的添加量为1.5g与0.05g。
54.将上述物质混合得到粘接膏体,采用丝网印刷方式将粘接膏体涂覆于铜板上,涂覆厚度为10um,涂覆完成后在80℃的条件下烘烤3分钟。
55.将将铝板与有粘接膏体一面的铜板对齐,并在高温和真空度为50mmhg的条件下进行压合。其中,压合时升温速度为5℃/min,最高温段为170℃,最高温段持续时间为30min,压合时的压力为15kg/cm2,压合时间为30min,升压时间为7min。压合完成后缓慢降温,降温速度为5℃/min。
56.降温完成后得到产品铜铝复合板。
57.实施例4
58.具体实施步骤与实施例3相同,只是最高温段持续时间为60min,压合时的压力为10kg/cm2,升压时间为5min。
59.实施例5
60.具体实施步骤与实施例3相同,只是导热导电粉体包括:粒径为5um的铜粉20g,粒径为3um的铝粉10g,粒径为1um的炭黑粉体10g,粒径为3um的炭黑粉体20g,粒径为2um的角型氧化铝10g。
61.实施例6
62.具体实施步骤与实施例3相同,只是最高温段为220℃,最高温段持续时间为45min。
63.实施例7
64.具体实施步骤与实施例3相同,粒径为9um的铜粉15g,粒径为7um的铜粉5g,粒径为3um的铝粉12g,粒径为2um的铝粉8g,粒径为1um的炭黑粉体20g,粒径为1um的角型氧化铝10g。
65.实施例8
66.具体实施步骤与实施例3相同,只是粒径为5um的铜粉15g,粒径为3um的铜粉5g,粒径为7um的铝粉12g,粒径为5um的铝粉8g,粒径为1um的炭黑粉体20g,粒径为1um的角型氧化铝10g。
67.实施例9
68.具体实施步骤与实施例3相同,只是铜粉的质量为导热导电粉体的50%。
69.导热导电粉体包括:粒径为5um的铜粉20g,粒径为3um的铜粉15g,粒径为2um的铝粉5g,粒径为1um的炭黑粉体20g,粒径为1um的角型氧化铝10g。
70.实施例10
71.具体实施步骤与实施例3相同,只是导热导电粉体中不包含有铜粉和铝粉。
72.导热导电粉体包括:粒径为1um的炭黑粉体20g,粒径为3um的炭黑粉体20g,粒径为1um的角型氧化铝20g,粒径为2um的角型氧化铝10g。
73.比较例1
74.具体实施步骤与实施例3相同,只是所述双酚a型酚醛环氧树脂为17.5g,即双酚a型酚醛环氧树脂和导热导电粉体的质量比为2.0:8.0。
75.实验例1
76.对实施例1-6以及比较例1-2的产品进行导热系数与结合力的测试,测试结果如下表所示:
77.[0078][0079]
现有技术中金属基线路板通常采用的散热方式是在灯珠等器件封装的背部加上金属凸台作为导体,将热量迅速的散发掉,该工艺中的金属凸台导体通常为铜。目前,铜铝复合板多是通过冷轧、热轧、爆炸复合法、爆炸轧制法等方式焊接在一起,其导热系数的范围多在2.0-5.0w/m
·
k之间。
[0080]
而本发明的铜铝复合板通过导热导电粉体和环氧树脂,在复合板之间形成了良好的导热通道和导电路径,如图1所示,粒径不同的粉体进行复配组合能够形成良好的导热通道,使得热量得到有效传导,导电性也得到提高,而根据粉体复配组合的方案不同,形成的导热通道也会有差别,如图1中的左右两边就无法形成良好的导热通道,散热性能较差。
[0081]
分析实验例的测试结果可知,采用本发明粘接组合物制备而得的铜铝复合板具有极佳的散热性能,导热系数大幅度提高。实施例1-5均是在本发明所提供的原料配比以及制备参数的范围内进行的,与实施例10未添加铜粉和铝粉的导热性能相比,实施例1-5的导热系数远高于实施例10的导热系数,说明本发明导热导电粉体中加入铜粉和铝粉生成的导热通道能显著提高产品的导热性能。另一方面,由于导电路径也是通过粉体之间的相互接触而形成的,导电率也有了明显提升。
[0082]
虽然实施例1-5均是在本发明的参数范围内制备,但是产品的导热系数、导电率和结合力也存在有一定的区别,这是因为原料之间的配比关系以及制备过程中的条件参数都会对导热性能、导电率和结合力产生影响。其中,实施例3为效果最好的实施例,其原料配比以及制备条件参数均为最优选的方案。与实施例3相比,实施例4主要的区别在于最高温段持续时间、压合压力以及升压时间,而实施例5的主要区别在于导热导电粉体之间的配比关系不同。而从实验结果来看,部分制备参数的不同以及导热导电粉体配比关系的不同,都会同时对导热系数和结合力产生影响,而要形成最佳的导热系数以及结合力,不仅需要合适的原料配比关系,还要搭配与该原料配比关系相适应的制备过程。
[0083]
另一方面,实验还测试了产品的厚度均匀性,厚度均匀性主要与制备过程中的条件参数有关,粘接层厚度均匀的铜铝复合板更稳定,不易出现分层、粘接不充分的情况。从上述测试结果可知,实施例3为效果最好的实施例,虽然实施例之间的厚度均匀性相差并不是很大,但要使产品达到使用更稳定的效果,仍是需要将制备过程中的条件参数设定在本发明所限定的合理范围内才能达到的。
[0084]
与实施例3相比,实施例6的测试结果较差,这是因为选用的固化温度过高所导致的,过高的温度会引起环氧树脂与粉体的分解,从而导致产品的导热系数和结合力下降。
[0085]
实施例7和实施例8与实施例3相比,区别在于采用的铜粉或铝粉的粒径过大。由于导热通道、导电路径是粉体之间相互接触而形成的,小粒径的粉体会填充在大粒径粉体之间的间隙中,从而与大粒径粉体形成更紧密的堆积,增加粉体之间的接触,从而提高产品的导热系数和导电率。而由于实施例7和实施例8的部分粉体粒径变大,那么与其他粒径的粉体的复配效果也会相应发生变化,实施例7和实施例8的导热系数,导电率均呈现一定程度的下降,分析是因为粉体间相互接触几率下降导致的,可见粒径的不同以及加入量的不同会对粉体在环氧树脂中的分布状态产生影响,从而影响导热通道的与导电路径形成,进而影响产品的导热系数与导电率。
[0086]
实施例9与实施例3相比,铜粉在导热导电粉体中的质量比过高,由于铜粉密度较大,在进行制备粘接膏体时,铜粉在膏体的内部出现了沉降的情况,无法形成良好的导热通道和导电路径,从而导致导热系数和导电率的变化较大,而由于粉体在环氧树脂中的分布不均一,经过高温压合后其结合力也会表现出小幅度的下降。
[0087]
比较例1与实施例3相比,所加入的双酚a型酚醛环氧树脂比例较少,对金属板的黏着力不够,在制备粘接膏体的过程中,粉体无法充分地被环氧树脂包裹,从而导致无法形成良好的导热通道,进而导致产品的导热系数和结合力均变化较大。
[0088]
综上所述,本发明公开了制备铜铝复合板的原料之间的配比关系以及制备过程中的条件参数,这些因素都不仅是影响产品的单一特性,也不是单一地对产品产生影响,这些因素之间存在有相互协同的关系,需要特定的、合理的配比关系才能兼顾结合力强、导热系数高、厚度均匀等效果。
[0089]
最后,可以理解的是,以上实施方式仅仅是为了说明本发明的原理而采用的示例性实施方式,然而本发明并不局限于此。对于本领域普通技术人员而言,在不脱离本发明的原理和实质的情况下,可以做出各种变型和改进,这些变型和改进也视为本发明的保护范围。