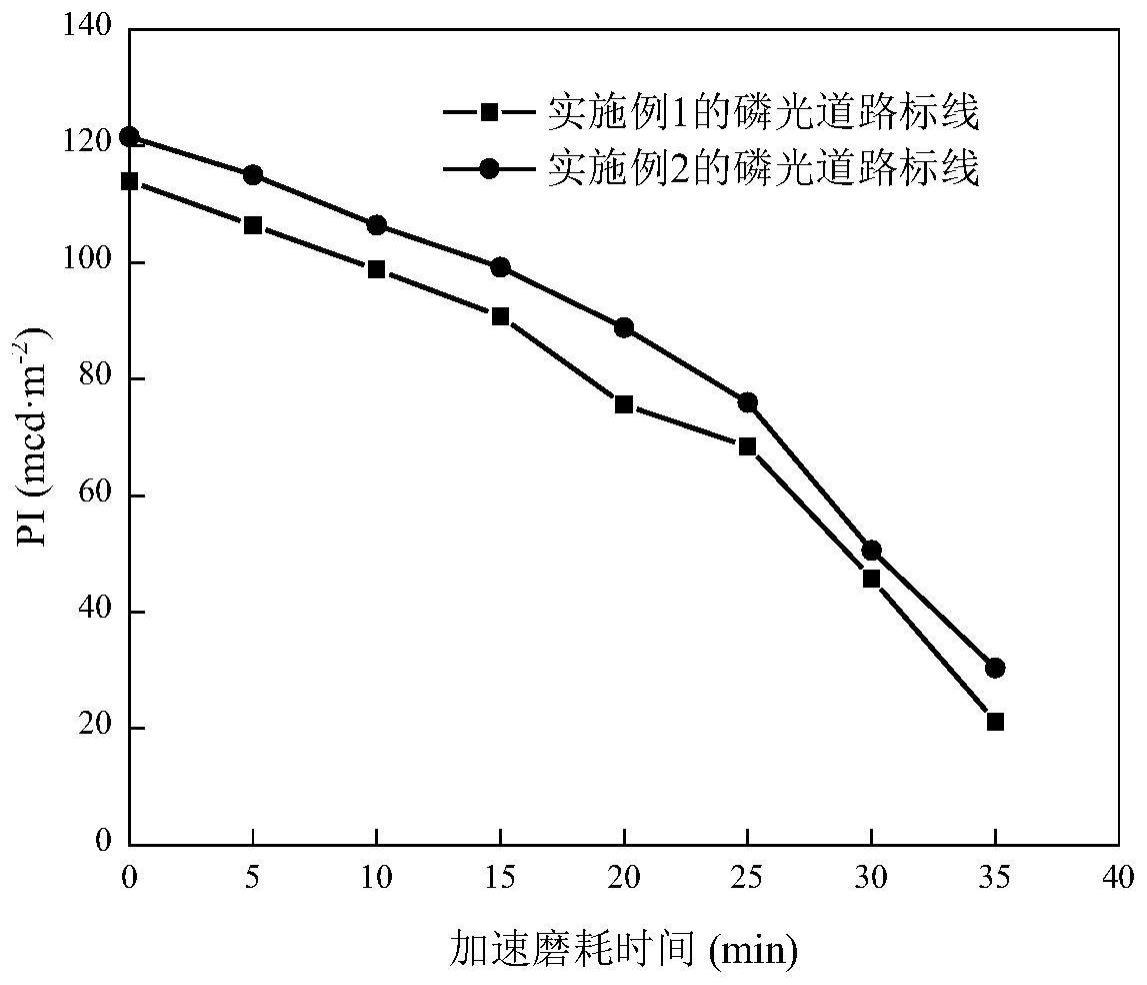
1.本发明涉及道路标线涂料及其制备和评价方法。
背景技术:2.道路标线是现代交通系统中最重要的组成部分,其视认性对驾驶安全至关重要,尤其是在夜间。据统计,夜间的交通事故率普遍高于白天,主要诱因为夜间交通标志标线的视认性低。传统的道路标线依靠嵌入的玻璃珠来提升视认性。然而,它们的施工质量难以控制,而且玻璃珠在车辆的磨损作用下容易脱落,这都对夜间驾驶安全构成了潜在的危险。为了解决传统道路标线的局限性,磷光道路标线(又称为荧光或者夜光道路标线)受到广泛关注。磷光道路标线是通过在道路标线材料中加入长余辉磷光粉制备而成。现有的磷光道路标线主要有热熔型、溶剂型、水性以及双组份型。热熔型磷光道路标线由于施工过程中需要加热,导致磷光粉的发光性能不佳,而且也会造成能源的消耗。溶剂型磷光标线在施工过程中会释放对环境有害的vocs,因而逐步受到限制。水性磷光标线具有绿色、环保、无污染等特点,但是其耐磨性能和耐久性不佳,导致使用寿命短。双组份磷光标线具有良好的耐磨性和耐久性,是当前应用较多的磷光标线。但是现有的双组份磷光标线采用的成膜树脂多为环氧树脂,但是环氧树脂中含有的环氧氯丙烷是一种有害的化合物,而且常温下易蒸发,因而会对环境造成危害。同时环氧树脂分子结构中含有苯环,导致磷光道路标线的抗紫外能力较弱、耐候性和耐久性普遍较差,在使用一段时间过后由于轮胎的磨耗作用,标线材料很快脱落。由于环氧树脂自身分子结构中含有的环氧氯丙烷和苯环,导致制备环保、耐久型环氧树脂基磷光道路标线成为难以解决的技术问题。此外对磷光道路的耐久性能也缺乏定量化且连续全面的相关评价措施。以上原因导致磷光道路标线的应用效果不佳。
技术实现要素:3.本发明是要解决现有的环氧树脂基磷光道路标线对环境危害大、耐久性差的技术问题,而提供一种无溶剂聚氨酯基磷光道路标线涂料及其制备和耐久性评价方法。
4.本发明的无溶剂聚氨酯基磷光道路标线涂料按质量份数比由165份无溶剂聚氨酯、20~83份磷光粉、14~17份钛白粉、50~66份重质碳酸钙和5~7份助剂组成;其中无溶剂聚氨酯为a、b双组分,其中a组分为多元醇,b组分为异氰酸酯,a组分与b组分的质量比为100:65;磷光粉为sral2o4:eu
2
,dy
3
;助剂为防沉降剂、光稳定剂、消泡剂和硅烷偶联剂。
5.更进一步地,助剂中按质量比,防沉降剂:光稳定剂:消泡剂:硅烷偶联剂=2:0.9:(0.6~0.7):(1.5~3.5)。
6.上述的无溶剂聚氨酯基磷光道路标线涂料的制备方法,按以下步骤进行:
7.一、按质量份数比称取165份无溶剂聚氨酯、20~83份磷光粉、14~17份钛白粉、50~66份重质碳酸钙和5~7份助剂;其中无溶剂聚氨酯为a、b双组分,a组分为多元醇,b组分为异氰酸酯,a组分与b组分的质量比为100:65;助剂为防沉降剂、光稳定剂、消泡剂和硅烷
偶联剂;
8.二、将无溶剂聚氨酯的a组分和b组分放在真空干燥箱中,在温度为25℃
±
2℃的条件下抽真空1~1.5h;目的是消除无溶剂聚氨酯中的气泡;
9.三、无溶剂聚氨酯a组分加入到分散机中,在分散机的转速为500~600r/min的条件下加入防沉降剂,加入完毕后,将分散机转速升高到1000~1200r/min,分散10~15min;然后将分散机转速降到500~600r/min,加入硅烷偶联剂、消泡剂、光稳定剂、磷光粉、钛白粉和重质碳酸钙,待所有原料加入完毕后,将分散机转速升高到1500r/min,分散20~30min;
10.四、将分散机转速降到200~300r/min,加入无溶剂聚氨酯的b组分,加入完毕后,分散5min,得到无溶剂聚氨酯基磷光道路标线涂料。
11.该无溶剂聚氨酯基磷光道路标线涂料的胶凝时间为20~40min,固化时间为12h,因此为了保证磷光道路标线具有良好的施工性能,制备好的磷光道路标线涂料应该在0.5h之内涂布在沥青路面上,得到磷光道路标线。
12.本发明的磷光道路标线的耐久性测试方法,按以下步骤进行:
13.一、磷光道路标线试件的制作:首先制作沥青混合料车辙板试件或水泥混凝土板试件作为标线的基材,试件尺寸为300mm
×
300mm
×
50mm;然后将无溶剂聚氨酯基磷光道路标线涂料涂布在试件表面,涂布尺寸为300mm
×
300mm,厚度为0.4~2.5mm,得到磷光道路标线试验件;同时用耐久性已知的白色热熔型道路标线涂料制备白色热熔型道路标线试验件,作为对照组;
14.二、测试磷光道路标线的初始发光强度:首先将磷光道路标线试验件在完全黑暗的地方放置24h,以消除其自身的初始能量;然后将其放置在1000lx的d65光源下照射10min;接着将其放置在黑暗的地方,等待至少10min,待其发光强度趋于稳定后,测试其发光强度,记为pi0。
15.白色热熔型道路标线的视认性通过逆反射亮度系数表征,测试白色热熔型道路标线的逆反射亮度系数,记为r
l0
;且要满足白色道路标线的初始逆反射亮度系数rl0不小于150mcd
·
m-2
·
lx-1
;
16.三、采用加速磨耗试验仪对磷光道路标线试验件和白色热熔型道路标线试验件进行磨耗,试验参数如下:温度为25℃
±
2℃、荷载为2.0kn
±
0.01kn、压强为0.15mpa
±
0.01mpa、轮胎转速为40rpm
±
3rpm、移动工作台运行速度为4.5次/min、洒水速度为35ml/min
±
5ml/min、金刚砂撒布速度为18g/min
±
3g/min、磨耗时间为5min/周期;
17.在每个磨耗周期结束后,将试件表面用水清洗干净、烘干,然后按照步骤二的方法分别测试磷光道路标线磨耗后的发光强度pic和白色热熔型道路标线磨耗后的逆反射亮度系数r
lc
,并按照式1计算发光强度衰退率,按式2计算逆反射亮度系数衰退率:
[0018][0019][0020]
当磷光道路标线发光强度衰退率δpi大于68%时,磷光道路标线磨耗试验结束,计算出衰退率δpi等于68%时的磨耗时间t1;当白色热熔型道路标线逆反射亮度系数衰退
率δr
l
大于68%时,白色热熔型道路标线的磨耗试验结束,计算出白色热熔型道路标线的衰退率等于68%时的磨耗时间t2;按式3算出磷光道路标线的使用寿命t;
[0021][0022]
式中t0为白色热熔型道路标线的使用寿命。
[0023]
本发明中,无溶剂聚氨酯是一种特殊的聚氨酯材料,其制备过程中直接将多元醇与异氰酸酯进行反应,不需要使用溶剂,因而具有绿色、环保、可持续等优点。与传统的道路标线相比,该无溶剂聚氨酯基磷光道路标线的优点如下:首先,磷光道路标线不需要撒布玻璃珠就能提供良好的视认性,所以本发明的涂料的施工工艺更简单,施工质量更容易控制。第二,磷光道路标线属于主动发光型道路标线,所以在夜间光线不足的路段提供更好的能见度和安全性。第三,磷光道路标线允许公路照明系统在其发光时间内关闭,从而节约能源。最后,磷光道路标线还具有环保性,因为它们使用的长余辉材料是可持续的,绿色的,对环境的污染较少,而传统的道路标线可能含有重金属,脱落的材料会造成污染。
[0024]
本发明还提供了一种磷光道路标线的耐久性评价方法,该方法采用加速磨耗试验仪对磷光道路标线进行磨耗,模拟其在实际使用过程中受到的轮胎磨耗作用,通过对磨耗前后磷光道路标线的发光性能的衰退情况对其耐久性进行评价。克服了现有的通过现场调研的方法评价磷光道路标线耐久性评价方法的试验条件不可控、无法指导磷光道路标线的材料设计及人力、物力、财力消耗量大的缺点。
[0025]
本发明的无溶剂聚氨酯基磷光道路标线涂料有施工工艺简单、夜间视认性好、耐久性好、绿色环保,可用于道路领域。
附图说明
[0026]
图1是实施例1中磷光道路标线磨耗后的发光强度pic随磨耗时间的变化情况图;
[0027]
图2是实施例1中白色热熔型道路标线磨耗后的逆反射亮度系数r
lc
随磨耗时间的变化情况图;
[0028]
图3是实施例1中磷光道路标线磨耗后的发光强度pic衰退率随磨耗时间的变化情况图;
[0029]
图4是实施例1中白色热熔型道路标线磨耗后的逆反射亮度系数r
lc
衰退率随磨耗时间的变化情况图。
具体实施方式
[0030]
用下面的实施例验证本发明的有益效果。
[0031]
实施例1:本实施例的无溶剂聚氨酯基磷光道路标线涂料的制备方法,按以下步骤进行:
[0032]
一、按质量份数比称取165份无溶剂聚氨酯、20.63份磷光粉、14.44份钛白粉、57.75份重质碳酸钙、2份防沉降剂、0.9份光稳定剂、0.6份消泡剂和2.5份硅烷偶联剂;
[0033]
其中无溶剂聚氨酯为a、b双组分,a组分为多元醇,b组分为异氰酸酯,a组分与b组分的质量比为100:65;无溶剂聚氨酯购自巴斯夫聚氨酯特种产品(中国)有限公司,a组分的产品名称c 6551/202c-a,b组分的产品名称elastopavec6551c-b;
[0034]
磷光粉为sral2o4:eu
2
,dy
3
,磷光粉sral2o4:eu
2
,dy
3
购自广州创嵘化工科技有限公司,型号为500目的疏水型长效黄绿光水性磷光粉;
[0035]
防沉降剂、光稳定剂、消泡剂、硅烷偶联剂均为助剂;
[0036]
二、将无溶剂聚氨酯的a组分和b组分放在真空干燥箱中,在温度为25℃的条件下抽真空1h;目的是消除聚氨酯中的气泡;
[0037]
三、无溶剂聚氨酯a组分加入到分散机中,在分散机的转速为500r/min的条件下加入防沉降剂,加入完毕后,将分散机转速升高到1000r/min,分散10min;然后将分散机转速降到500r/min,加入硅烷偶联剂、消泡剂、光稳定剂、磷光粉、钛白粉和重质碳酸钙,待所有原料加入完毕后,将分散机转速升高到1500r/min,分散20min;
[0038]
四、将分散机转速降到300r/min,加入无溶剂聚氨酯的b组分,加入完毕后,分散5min,得到无溶剂聚氨酯基磷光道路标线涂料。
[0039]
实施例2:本实施例与实施例1不同的是步骤一中按质量份数比称取165份无溶剂聚氨酯、82.5份磷光粉、16.5份钛白粉、66份重质碳酸钙、2份防沉降剂、0.9份光稳定剂、0.7份消泡剂和3.3份硅烷偶联剂;其它步骤与参数与实施例1相同。
[0040]
将实施例1和实施例2制备的无溶剂聚氨酯基磷光道路标线涂料进行磷光道路标线的耐久性测试,具体的方法按以下步骤进行:
[0041]
一、磷光道路标线试件的制作:首先制作沥青混合料车辙板试件作为标线的基材,试件尺寸为300mm
×
300mm
×
50mm;然后将无溶剂聚氨酯基磷光道路标线涂料涂布在试件表面,涂布尺寸为300mm
×
300mm,厚度为2mm,得到磷光道路标线试验件;同时用市售白色热熔型道路标线涂料涂布在相同级配的沥青混合料车辙试件表面,作为对照组,该市售白色热熔型道路标线涂料的耐久性已知,耐久性为15个月;
[0042]
二、测试磷光道路标线的初始发光强度:首先将磷光道路标线试验件在完全黑暗的地方放置24h,以消除其自身的初始能量;然后将其放置在1000lx的d65光源下照射10min;接着将其放置在黑暗的地方,等待10min,待其发光强度趋于稳定后,测试其发光强度,记为pi0。其中实施例1的涂料制备的磷光道路标线的初始发光强度为114mcd
·
m-2
,实施例2的涂料制备的磷光道路标线的初始发光强度为121.6mcd
·
m-2
;
[0043]
三、白色热熔型道路标线的视认性通过逆反射亮度系数表征,测试白色热熔型道路标线的逆反射亮度系数,记为r
l0
;r
l0
=198.8cd
·
lx-1
·
m-2
,满足gb/t 16311白色道路标线的初始逆反射亮度系数应不小于150mcd
·
m-2
·
lx-1
的要求;
[0044]
四、采用加速磨耗试验仪对磷光道路标线试验件和白色热熔型道路标线试验件进行磨耗,试验参数如下:温度为25℃
±
2℃、荷载为2.0kn
±
0.01kn、压强为0.15mpa
±
0.01mpa、轮胎转速为40rpm
±
3rpm、移动工作台运行速度为4.5次/min、洒水速度为35ml/min
±
5ml/min、金刚砂撒布速度为18g/min
±
3g/min、磨耗时间为5min/周期;
[0045]
在每个磨耗周期结束后,将试件表面用水清洗干净、烘干,然后按照步骤二的方法分别测试磷光道路标线磨耗后的发光强度pic和白色热熔型道路标线磨耗后的逆反射亮度系数r
lc
,并按照式1计算发光强度衰退率,按式2计算逆反射亮度系数衰退率:
[0046]
[0047][0048]
当白色热熔型道路标线逆反射亮度系数衰退率δr
l
大于68%时,白色热熔型道路标线的磨耗试验结束;当磷光道路标线发光强度衰退率δpi大于68%时,磷光道路标线磨耗试验结束;磷光道路标线磨耗后的发光强度pic随磨耗时间的变化情况如图1所示;白色热熔型道路标线磨耗后的逆反射亮度系数r
lc
随磨耗时间的变化情况如图2所示;磷光道路标线磨耗后的发光强度pic衰退率随磨耗时间的变化情况如图3所示;白色热熔型道路标线磨耗后的逆反射亮度系数r
lc
衰退率随磨耗时间的变化情况如图4所示。
[0049]
计算出两个磷光道路标线试件当发光强度衰退率达到68%的时间均为35min,即磷光道路标线的磨耗时间t1为35min;白色热熔型道路标线的逆反射亮度系数衰退率达到68%的时间为30min,即白色热熔型道路标线的磨耗时间t2为30min;按式3算出磷光道路标线的使用寿命t为17.5个月;
[0050][0051]
式中t0为白色热熔型道路标线的使用寿命;t0为15个月;
[0052]
热熔型道路标线的视认性主要由撒布在其表面的玻璃珠提供,然而,由于玻璃珠与热熔型道路标线的相容性不佳以及玻璃珠本身的强度不足,导致玻璃珠在交通荷载的作用下容易发生脱落和破碎,使道路标线的逆反射性能迅速衰退,从而对道路标线的耐久性产生不利影响,这给提升热熔型道路标线的耐久性带来极大的困难,而本发明克服了玻璃珠与热熔型道路标线的相容性不佳以及玻璃珠本身的强度不足的影响,而利用无溶剂聚氨酯基磷光道路标线涂料中磷光粉与基体涂料的粘结强度高,从而提高其耐久性,通过实施例1和实施例2的相关数据说明,本发明中磷光道路标线的耐久性优于市售的白色热熔型道路标线的耐久性。白色热熔型道路标线的耐久性为15个月。因此在相同的工况下,两种磷光道路标线的耐久性可达到17.5个月,比白色热熔型道路标线的耐久性提高了17%。