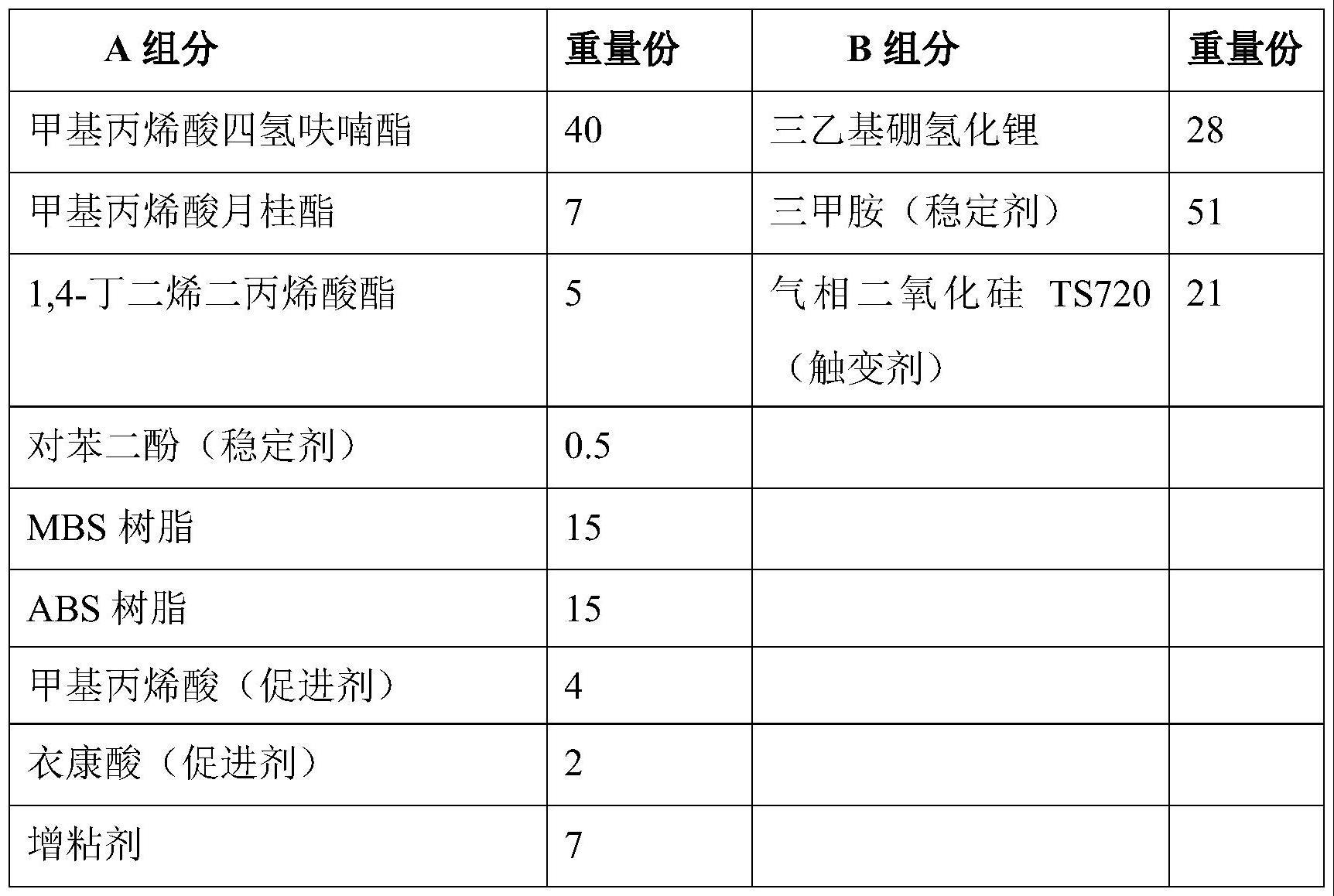
1.本发明属于胶黏剂领域,具体涉及一种丙烯酸酯胶黏剂及其制备方法和应用。
背景技术:2.低表面能材料,如pe、pp、pa、pi、tpo、ptfe、pet、pbt等,表面能低,结晶度高,无法被溶剂溶胀,表面无法润湿,现有的胶粘剂对这些材料很难起作用。通常采用电晕、等离子、火焰处理表面,需要在有效时间内快速贴合,超过时间粘接效果会大幅下降,采用这类处理方法难免会有遗漏或者不均匀的情况发生,导致粘接强度分布不均匀,甚至开胶情况。有的甚至使用更高毒性的溶剂,如氯仿等,进行表面处理,对环境和人体造成毒害。也有采用直接贴双面胶带的方案,但强度达不到使用环境的要求。随着社会发展,这些材料越来越多的被人们所使用,但对于这类材料的粘接目前仍没有更直接、更有效的办法。对这类胶黏剂产品的需求较为迫切,为弥补市场上产品缺少,开发出一种用于低表面能材料粘接的低气味型胶黏剂已尤显必要。
技术实现要素:3.本发明所要解决的技术问题是,克服以上背景技术中提到的不足和缺陷,提供一种用于低表面能材料粘接的丙烯酸酯胶黏剂及其制备方法和应用。
4.为解决上述技术问题,本发明提出的技术方案为:
5.一种丙烯酸酯胶黏剂,所述丙烯酸酯胶黏剂由a组份和b组份组成;
6.所述a组分的制备原料包括按重量份计的下述组分:丙烯酸酯类单体45份~75份、增韧树脂15份~45份、稳定剂0.02份~3份、促进剂1份~10份、增粘剂1份~10份和触变剂0.5~10份;
7.所述b组分的制备原料包括按重量份计的下述组分:烷基金属硼氢化物20份~40份、稳定剂20份~60份和触变剂5份~30份;
8.其中,a组份和b组份质量比为(8~15):1。
9.作为进一步的改进,所述增韧树脂选自核壳型结构的mbs树脂、abs树脂或丙烯酸酯树脂中的一种或任意组合。
10.作为进一步的改进,所述a组分中的稳定剂选自对苯二酚、1,4-萘醌、氢醌、叔丁基对苯二酚或吩噻嗪中的一种或任意组合;和/或
11.所述b组分中的稳定剂选自三甲胺、三乙胺、三丙胺的一种或任意组合。
12.作为进一步的改进,所述促进剂选自巴豆酸、衣康酸、巴比妥酸或甲基丙烯酸中的一种或任意组合。
13.作为进一步的改进,所述增粘剂为含氟异氰酸酯与含羟基的丙烯酸单体共聚物。
14.作为进一步的改进,所述含氟异氰酸酯与含羟基的丙烯酸单体共聚物的制备方法为,将含氟异氰酸酯与含羟基的丙烯酸单体反应至nco%≤0.05%。
15.作为进一步的改进,所述含氟异氰酸酯选自邻氟异氰酸酯、间氟异氰酸酯或对氟
异氰酸酯中的一种或任意组合;和/或,所述含羟基的丙烯酸单体选自甲基丙烯酸羟乙酯和/或甲基丙基酸羟丙酯。
16.作为进一步的改进,所述烷基金属硼氢化物选自三乙基硼氢化锂、三乙基硼氢化钾或三乙基硼氢化钠中的一种或任意组合。
17.本发明还提供一种所述丙烯酸酯胶黏剂的制备方法,包括下述的步骤:
18.a组分的制备:将丙烯酸酯类单体、稳定剂和增韧树脂搅拌溶解,再加入促进剂、增粘剂并搅拌均匀,最后加入触变剂并搅拌均匀,即得a组分;
19.b组分的制备:在惰性气体保护下,在搅拌下将稳定剂加入到烷基金属硼氢化物中,温度控制在20~30℃,搅拌1.5~2.5h,然后在惰性气体保护加入触变剂并搅拌均匀,即得b组分。
20.本发明还提供一种所述丙烯酸酯胶黏剂在粘接低表面能材料中的应用。
21.与现有技术相比,本发明的有益效果为:
22.(1)本发明采用的引发剂烷基金属硼氢化物,会从低表面能待粘接材料表面开始引发自由基聚合,又可减少界面应力的产生,因此低表面能基材无需处理,直接粘接使用即可并且粘接强度高,简化了装配流程,节省时间,提高制造效率;同时,烷基金属硼氢化物在引发过程中吸收氧气,所以也解决了低气味胶黏剂表面受氧阻聚发粘问题;
23.(2)本发明引入含氟异氰酸酯与含羟基的丙烯酸单体共聚物作为增粘剂,进一步降低胶体本身的表面张力,使得对低表面能的粘接强度更高、更稳定;
24.(3)本发明用于低表面能材料粘接的丙烯酸酯胶黏剂,粘接强度高,使用方便,环保、气味低,不会对人和环境的产生危害。
具体实施方式
25.为了便于理解本发明,下文将结合较佳的实施例对本发明做更全面、细致地描述,但本发明的保护范围并不限于以下具体实施例。
26.除非另有定义,下文中所使用的所有专业术语与本领域技术人员通常理解含义相同。本文中所使用的专业术语只是为了描述具体实施例的目的,并不是旨在限制本发明的保护范围。
27.除非另有特别说明,本发明中用到的各种原材料、试剂、仪器和设备等均可通过市场购买得到或者可通过现有方法制备得到。
28.本发明一些具体实施方式的丙烯酸酯胶黏剂,由a组份和b组份组成。
29.其中a组分的制备原料包括按重量份计的下述组分:丙烯酸酯类单体45份~75份(优选45~60份)、增韧树脂15份~45份(优选20~40份)、稳定剂0.02份~3份(优选0.1~1份)、促进剂1份~10份(优选4~8份)、增粘剂1份~10份(优选5~10份)和触变剂0.5~10份(优选3~8份)。
30.其中b组分的制备原料包括按重量份计的下述组分:烷基金属硼氢化物20份~40份(优选25~35份)、稳定剂20份~60份(优选40~60份)和触变剂5份~30份(优选15~25份)。
31.在一些具体实施例中,a组份和b组份质量比(8~15):1。
32.在一些具体实施方式中,所述丙烯酸酯类单体选自:低气味的2-苯氧乙基甲基丙
烯酸酯、甲基丙烯酸异辛酯、甲基丙烯酸月桂酯、甲基丙烯酸四氢呋喃酯、三环癸烷二甲醇二丙烯酸酯、乙氧化双份a二甲基丙烯酸酯、1,4-丁二烯二丙烯酸酯、环氧丙烯酸树脂或聚氨酯丙烯酸树脂中的一种或几种。
33.在一些具体实施方式中,所述增韧树脂选自核壳型结构的mbs树脂、abs树脂或丙烯酸酯树脂中的一种或几种。
34.在一些具体实施方式中,a组分中的稳定剂选自对苯二酚、1,4-萘醌、氢醌、叔丁基对苯二酚或吩噻嗪中的一种或几种。
35.在一些具体实施方式中,所述促进剂选自巴豆酸、衣康酸、巴比妥酸、甲基丙烯酸中的一种或几种。通过酸性强弱和用量控制,可以对固化速度进行调节(酸性增强,固化速度变快),得到不同固化速度的产品,使得反应固化速度具有可调节性,以满足大小不同工件的粘接需求。在一些具体实施例中,促进剂采用甲基丙烯酸和衣康酸,二者质量比(1.8~2.2):1,初固时间10min左右(2g胶液中心部位变硬的时间定义为初固时间)。
36.在一些具体实施方式中,所述增粘剂为含氟异氰酸酯与含羟基的丙烯酸单体共聚物,采用该增粘剂进一步降低胶体本身的表面张力,使得对低表面能的粘接强度更高、更稳定。在一些具体实施例中,所述的含氟异氰酸酯与含羟基的丙烯酸单体共聚物的制备方法为,将含氟异氰酸酯与含羟基的丙烯酸单体反应至nco%≤0.05%。在一些具体实施例中,所述的含氟异氰酸酯选自邻氟异氰酸酯、间氟异氰酸酯、对氟异氰酸酯中的一种或几种。所述的含羟基的丙烯酸单体选自甲基丙烯酸羟乙酯或甲基丙基酸羟丙酯中的一种或几种。优选的,含氟异氰酸酯与含羟基的丙烯酸单体摩尔比为(0.95~1.05):1。优选的,反应时间为5~7h。
37.在一些具体实施方式中,所述a组分和b组分中的触变剂均可采用疏水性表面的气相二氧化硅,如ts720或h2000中的一种或几种。
38.在一些具体实施方式中,所述烷基金属硼氢化物选自三乙基硼氢化锂、三乙基硼氢化钾或三乙基硼氢化钠中的一种或几种。a组分和b组分混合施胶后,烷基金属硼氢化物作为引发剂,会从低表面能待粘接材料表面开始引发自由基聚合,又可减少界面应力的产生,因此低表面能基材无需处理,直接粘接使用即可。同时,烷基金属硼氢化物在引发过程中吸收氧气,所以也解决了低气味胶黏剂表面受氧阻聚发粘问题。
39.在一些具体实施方式中,所述b组分中的稳定剂选自三甲胺、三乙胺、三丙胺的一种或几种。该稳定剂的作用是,制备过程中形成稳定的硼胺络合物,以稳定硼氢化物,与a组分混合后,释放出可引发聚合的硼化合物,进一步产生自由基聚合反应。
40.本发明一些具体实施方式的丙烯酸酯胶黏剂制备方法,包括下述的步骤:
41.a组分的制备:将丙烯酸酯类单体、稳定剂和增韧树脂搅拌使之充分溶解,再加入促进剂、增粘剂搅拌均匀,最后加入触变剂,搅拌均匀,即得a组分。
42.b组分的制备:在惰性气体保护下,边搅拌边将稳定剂加入到烷基金属硼氢化物中,优选温度控制在20~30℃,优选密封搅拌1.5~2.5h;然后在惰性气体保护加入触变剂,搅拌均匀,即得b组分。
43.在使用时,a组份和b组份按质量比(8~15):1进行混合后施胶。
44.实施例1
45.本实施例的丙烯酸酯胶黏剂,制备原料如表1所示。
46.表1
[0047][0048][0049]
其中,增粘剂制备方法为:将0.2mol邻氟异氰酸酯与甲基丙烯酸羟乙酯投入到反应釜中,搅拌6h,测试nco%≤0.05%,停止搅拌,即得该共聚物。
[0050]
本实施例的丙烯酸酯胶黏剂的制备方法为:
[0051]
a组分制备:将甲基丙烯酸四氢呋喃酯、甲基丙烯酸月桂酯、1,4-丁二烯二丙烯酸酯、对苯二酚、mbs树脂、abs树脂加入到搅拌釜中,进行充分溶解,再加入甲基丙烯酸和衣康酸、自制增粘剂搅拌均匀,最后加入气相二氧化硅ts720,搅拌均匀,真空除泡,即得a组分。
[0052]
b组分制备:将三乙基硼氢化锂加入到搅拌釜中,氮气保护情况下边搅拌边加入三甲胺搅拌过程通冷水控温在20~30℃,密封搅拌2h;在氮气保护情况下加入气相二氧化硅ts720,搅拌均匀真空除泡,即得b组分(密闭存储)。
[0053]
将a组分和b组分按照10:1比例混合。
[0054]
实施例2
[0055]
本实施例的丙烯酸酯胶黏剂,制备原料如表2所示。本实施例增粘剂制备方法,丙烯酸酯胶黏剂的制备方法,以及a组分和b组分比例均与实施例1相同。
[0056]
表2
[0057][0058]
实施例3
[0059]
本实施例的丙烯酸酯胶黏剂,制备原料如表3所示。本实施例增粘剂制备方法,丙烯酸酯胶黏剂的制备方法,以及a组分和b组分比例均与实施例1相同。
[0060]
表3
[0061]
[0062]
对比例1
[0063]
本对比例的丙烯酸酯胶黏剂,制备原料如表4所示。本对比例丙烯酸酯胶黏剂的制备方法,以及a组分和b组分比例均与实施例1相同,不同之处仅在于不添加增粘剂。
[0064]
表4
[0065][0066]
性能测试
[0067]
根据gb/t 7124-2008测试胶粘剂的剪切强度,具体性能结果见表5。其中,2g胶液中心部位变硬的时间定义为初固时间。
[0068]
表5
[0069][0070]
由上表可看到:市售的胶带和丙烯酸酯结构胶对低表面能基材粘接力都很小,经过电晕处理后,粘结力大幅提升,而采用实施例1样胶粘接后,与电晕处理的粘接效果相当;对于中等表面张力的abs和pc基材粘接实施例1与其它两种性能一致;对于金属基材(al)粘接实施例1强度略有下降,可能是本体系只针对低表面能基材粘接而设计。
[0071]
上述只是本发明的较佳实施例,并非对本发明作任何形式上的限制。因此,凡是未脱离本发明技术方案的内容,依据本发明技术实质对以上实施例所做的任何简单修改、等同变化及修饰,均应落在本发明技术方案保护的范围内。