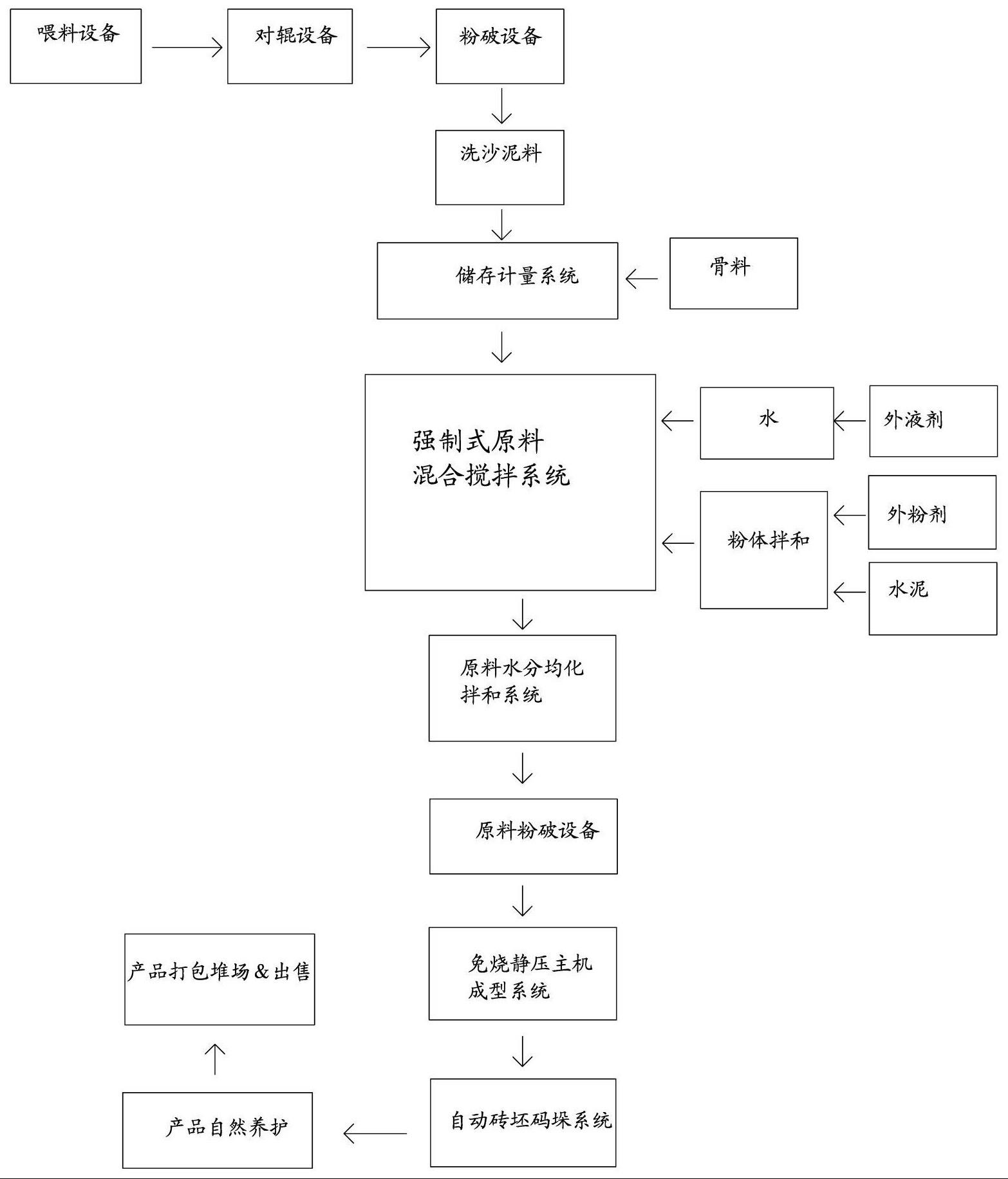
1.本发明涉及一种含有水泥材料的混合物的技术领域,特别是涉及一种洗沙泥基的水泥混合材料及其成型方法。
背景技术:2.随着我国2019年颁布禁采天然河沙的法令实措,导致市场经济对砂石集骨材料需求连续不断地增长及经济价值不断升高,而形成另一新的机制砂洗沙行业诞生。
3.根据中国砂集骨材料网数据显示,我国全年用沙量达180亿吨,每年全国机制砂产量达45亿吨,按机制砂洗沙含泥量20%左右计算,每年将产生洗沙泥多达9亿吨,按5万吨占地2亩计算,其需土地堆场1.8万亩。
4.长三角区域每年河道清淤洗沙泥料达8000万立方。按传统处置法露天堆放,填埋,烧结红砖。由于洗沙泥含水率高,泥料颗粒粒细,按传统处置法将对周边生态环境造成污染;且用在烧结红砖掺配量低,烧结能耗大,综合性价比高,并且国家在1993年早已颁布法律法规禁止烧结粘土砖。
5.近年来,市场形成以泥土固化技术来处理弃泥的新技术,其固化技术只能解决湿泥固化脱降水,或弃泥固化制砖,但其存在强度低、耐水性差及掺配量小等问题,其中,强度和耐水性等都难以达到国家行业标准,同时所添加固化剂与外加脱水剂(有机絮凝剂)相互冲突,无法实现终端产品的市场推广性、经济性的终极目标。
6.具体如现有市场所推行的弃泥免烧制砖存在诸多问题包括产品掺合量低(20%~30%),产品强度低(6~8mpa),耐水性差(浸泡水易松脱或脱皮),产品密实度低,吸水率高(20%~30%),产品软化系数低(0.5~0.7),且产品生产工艺设计有缺陷不完整,不能将各原材料完全均化,导致制成的成型产品开裂,压实度不够,吸水率高,抗冻性差等问题。
7.有鉴于此,发明人进行深入研究,遂有本发明的产生。
技术实现要素:8.本发明的目的在于提供一种可提高弃泥掺合量,并且可解决免烧砖产品质量问题的洗沙泥基的水泥混合材料及其成型方法。
9.为了达成上述目的,本发明的技术方案是:一种洗沙泥基的水泥混合材料,所述水泥混合材料为免烧砖,包括如下原料:以重量份计,洗沙泥料70~85份、集骨材料10~30份、胶凝材料8~25份、早强速凝材料0.5~6份,表面活性材料0.1~5.0份、激发促进材料0.1~6.0份和水2-8份;所述胶凝材料、所述早强速凝材料、所述表面活性材料和所述激发促进材料组成外添加复合材料,所述外添加复合材料为包括固体试剂与液体试剂结合使用的混合试剂,所述固体试剂为粉体试剂;所述洗沙泥料中,颗粒粒径为5~10mm的泥料占3%~5%,颗粒粒径≤3mm的泥料占70%~90%,颗粒粒径为3~5mm的泥料占10%~20%;
所述洗沙泥料的含水率为6%~15%;所述集骨材料中,颗粒粒径为10~15mm的材料占5%,颗粒粒径为5~10mm的材料占10~15%,颗粒粒径≤5mm的材料占60~80%;所述早强速凝材料包括甲酸钙,三乙醇胺,硅钢素醚,硫酸钠,元明粉和自制复合早强剂中的一种或多种组合,所述自制复合早强剂包括硫酸铝、二氧化硅、氧化铝、s95矿粉和硅微粉 ,所述早强速凝材料中的液态原材料的含固量为15%~30%,所述早强速凝材料中的粉体原材料的细度为300~500目,比表面积大于2400~2900m
²
/g;所述表面活性材料包括减水剂pc-1009,憎水剂kh151,防水剂n-2和纤维素醚中的至少一种,所述表面活性材料中的液态原材料的含固量为15%~20%,粉体原材料的细度为200~350目,比表面积大于1800~2400m
²
/g,且溶于水;所述激发促进材料包括碱激发剂和/或硫酸盐激发剂,所述碱激发剂包括氢氧化钠、氢氧化钾和水玻璃中的一种或多种组合,所述硫酸盐激发剂包括硫酸钠和/或硫酸钾,所述激发促进材料中各原材料的纯度为75%~95%;所述胶凝材料包括普硅水泥,矿渣水泥,粉煤灰水泥和硫铝酸盐水泥,所述胶凝材料的质量符合国家行业标准《gb175-2020》。
10.进一步地,所述集骨材料制砖包括瓜子石,05石,破碎建筑垃圾集骨材料和矿石破碎边角料中的至少一种。
11.一种洗沙泥基的水泥混合材料的成型方法,制备过程中所用制砖系统包括:泥料来料预置系统,原料仓储计量系统,原料混合搅拌系统,原料水分陈化均化拌和系统,原料均化粉破系统,免烧静压成型制砖系统,自动砖坯码垛系统和产品养护系统;所述免烧砖的制砖方法包括如下步骤:步骤s1,泥料来料预置处理:使用泥料来料预置系统将含水率为8~15%的洗沙泥料转移至喂料机进行均匀给料,然后将洗沙泥料输送至对辊机进行集骨材料破碎与泥料辊压变薄处理,对辊间距调整为0.5~10mm;对辊处理过的洗沙泥料用皮带输送至粉破机进行洗沙泥料的粉破与打散处理,粉破后的洗沙泥料中,颗粒粒径为≤3mm的部分占80%,以及颗粒粒径为3~8mm的部分占20%;步骤s2,原料仓储计量处理:使用原料仓储计量系统设定plc电控参数并控制储料仓各原料计量数与传送,其中,原料计量包括符合颗粒级配的洗沙泥料,其掺配比占75~80%;集骨材料,其掺配比占5~15%,集骨材料符合颗粒级配,颗粒径≤5mm的部分占80%,5~10mm的部分占15%,以及10~15mm的部分占5%;然后将步骤s1粉破机破碎好的洗沙泥料由皮带输送至储料仓存储,集骨材料由铲车从集骨材料堆场转移至储料仓;由plc电控操作皮带电子感应称进行洗沙泥料和集骨材料的分别计量;同时设定plc电控参数并控制各电子感应称进行各其他原料的分别计量并输送至原料混合搅拌系统,其中,水,掺配量为2~8%、胶凝材料水泥,掺配量为8~15%,以及余下其他外添加复合材料,掺配量为0.05%;步骤s3,原料混合搅拌处理:使用原料混合搅拌系统将原料仓储计量系统计量得到的计量原料进行半干法混合搅拌,搅拌时间2~3min,转速25~35t/min;将各计量原料先在强制式混合搅拌机内进行粉体原料的混合搅拌,将粉体原料干拌和,拌和时间2min,再用雾化喷淋加水湿法拌和,拌和时间1~1.5min,混合搅拌后得到半
干湿原料,接着将所述半干湿原料输送至原料水分均化拌和系统;步骤s4,原料水分均化拌和处理:使用原料水分均化拌和系统将步骤s3的半干湿原料再次进行均化拌和搅拌,拌和时间2~3min,转速20~30t/min,让半干湿原料颗粒表面在加水湿化后使水分子更加均匀地附着在泥颗粒表面并陈化渗透,将再次拌和好的加湿均化混合原料输送至原料均化粉破系统;步骤s5,原料均化粉破处理:使用原料均化粉破系统将步骤s4的加湿均化混合原料进行破碎,至无成团集块,破碎所用的原料粉破机运行转速120~140t/min,每小时处理破碎原料50~100t,混合原料粉破后输送至免烧静压成型制砖系统;步骤s6,免烧静压成型制砖处理:使用免烧静压成型制砖系统将步骤s5均化粉破处理后的原料进行免烧砖坯挤压成型;挤压成型工艺流程的操作顺序依次为:混合原料储存、布料车搅拌与布料、上下挤头与模框素互锁联动完成砖坯成型、以及夹砖器抱送成型砖坯至输送皮带;步骤s7,自动砖坯码垛处理:使用自动砖坯码垛系统将步骤s6的成型砖坯进行砖板码垛堆放;步骤s8,产品养护处理:使用产品养护系统将步骤s7码垛后的成品砖坯进行养护期内无洒水自然养护,养护后得到的砖平均符合国家行业mu10~mu20标准。
12.进一步地,步骤s6中,所述布料车内设三联机械搅拌结构设计,布料时,将混合原料布料于模具腔内,同时利用所述三联机械搅拌结构将混合原料进行再次拌和均化,并且在下料的同时形成挤压布料。
13.进一步地,步骤s3中,所述原料混合搅拌系统包括强制式混合搅拌设备,以及用于喷洒水分或外添加复合材料中液体试剂的加湿雾化双组交错喷头组件,所述加湿雾化双组交错喷头组件包括交错喷头,所述交错喷头交错安装并呈45度角分布焊接在一条直线管道上;喷洒时,所述交错喷头将液体均化喷洒至所述强制式混合搅拌设备的搅拌原料上。
14.进一步地,步骤s8中,所述产品养护处理时,成品砖坯由叉车转移至厂棚养护区进行自然养护或养护窑恒温养护;所述厂棚为阳光板房,其内增设加湿雾化喷淋装置,在气温达35~40度时启用加湿空气养护;所述养护窑恒温养护为在恒温恒湿条件下养护砖坯产品,恒温在35~45度,相对湿度75~90%,连续1~2天养护。
15.采用上述方案后,本发明一种洗沙泥基的水泥混合材料,即一种洗沙泥基免烧砖,具有以下有益效果:可实现弃泥固废原料100%资源再生利用,产品质量强度达到国家行业标准(符合mu10~mu20标准),弃泥(即洗沙泥)掺配量达到≥80%,为业内最高。耐水性即抗冻融性符合15次~25次循环检测,同时弃泥免烧制生态环保砖不仅解决了土地占用问题,同时还解决生态环保问题。
16.本发明一种洗沙泥基的水泥混合材料(免烧砖)的成型方法,具有如下有益效果:能将洗沙泥100%资源再生利用。经过本发明制砖系统成型,同时配合免烧砖的主材料及外添加复合剂,从而可保证洗沙泥免烧砖产品的高致密性,降低砖体毛细孔率,减少吸水率
(≤15%),提高产品软化系数(≥0.8)和耐水性能(抗冻融测试10~25次),最大实现洗沙泥掺配量(≥80%),是一种低成本(0.18~0.25元/块),压实度致密,高强度(mu10~mu20),耐候性好的环保节能免烧泥砖。
附图说明
17.图1为本发明的一种洗沙泥基免烧砖的成型方法的流程图。
18.图中:外液剂为外添加复合材料中的液体试剂;外粉剂为除去胶凝物质水泥外的外添加复合材料中的粉体试剂。
具体实施方式
19.为了进一步解释本发明的技术方案,下面通过具体实施例来对本发明进行详细阐述。
20.实施例1本发明一种洗沙泥基的水泥混合材料,本发明中,水泥混合材料为免烧砖,包括如下原料:以重量份计,洗沙泥料70~85份、集骨材料10~30份、胶凝材料8~25份、早强速凝材料0.5~6份,表面活性材料0.1~5.0份、激发促进材料0.1~6.0份和水2-8份;所述胶凝材料、所述早强速凝材料、所述表面活性材料和所述激发促进材料组成外添加复合材料,所述外添加复合材料为包括固体试剂与液体试剂结合使用的混合试剂,所述固体试剂为粉体试剂;所述洗沙泥料中,颗粒粒径为5~10mm的泥料占3%~5%,颗粒粒径≤3mm的泥料占70%~90%,颗粒粒径为3~5mm的泥料占10%~20%;所述洗沙泥料的含水率控制在6%~15%;所述集骨材料中,颗粒粒径为10~15mm的部分占5%,颗粒粒径为5~10mm的部分占10~15%,颗粒粒径≤5mm的部分占60~80%;所述早强速凝材料包括甲酸钙,三乙醇胺,硅钢素醚,硫酸钠,元明粉和自制复合早强剂中的一种或多种组合,所述自制复合早强剂包括硫酸铝、二氧化硅、氧化铝、s95矿粉和硅微粉,所述早强速凝材料中的液态原材料的含固量为15%~30%,所述早强速凝材料中的粉体原材料的细度为300~500目,比表面积大于2400~2900m
²
/g;所述表面活性材料包括减水剂,憎水剂,防水剂和纤维素醚中的至少一种,所述表面活性材料中的液态原材料的含固量为15%~20%,粉体原材料的细度为200~350目,比表面积大于1800~2400m
²
/g,且溶于水;本发明中,防水剂,憎水剂和减水剂均采用建筑工程行业内公知的相应试剂,以能实现相应的功能即可,在此不予限定。本发明所用的防水剂,憎水剂和减水剂均为市场上购买的相应产品。本实施例中,纤维素醚具体型号:羟丙基甲基纤维(hpmc),生产商:戈麦斯化工(中国)有限公司;防水剂具体型号:sn-2 生产商:山东双牛化工科技有限公司;憎水剂具体型号:kh151 生产商:山东沅锦新材料有限公司;减水剂具体型号:pc-1009 生产商:武汉华轩高新技术有限公司。所述激发促进材料包括碱激发剂和/或硫酸盐激发剂,所述碱激发剂包括氢氧化钠、氢氧化钾和水玻璃中的一种或多种组合,所述硫酸盐激发剂包括硫酸钠和/或硫酸钾,所述激发促进材料中各原材料的纯度为75%~95%。
21.作为一种优选地实施方式,以重量份计,所述自制复合早强剂包括硫酸铝30~40
份、二氧化硅5-10份、氧化铝20~30份、s95矿粉5~10份和硅微粉50~60份。
22.作为一种优选地实施方式,所述集骨材料制砖包括瓜子石,05石,破碎建筑垃圾集骨材料和矿石破碎边角料中的至少一种;所述胶凝材料包括普硅水泥,矿渣水泥,粉煤灰水泥和硫铝酸盐水泥,所述胶凝材料的质量要求符合国家行业标准如《gb175-2020》。
23.作为一种优选地实施方案,外添加复合材料a组分材料配置:以重量份计,称取早强速凝材料0.5份;表面活性材料0.5份;激发促进材料1.5份 和胶凝材料15份,将各组分拌合均化后,得到洗沙泥基免烧砖的外添加复合材料a组分原料;本发明一种洗沙泥基免烧砖(下文称为方案a),以重量份计,包括洗沙泥原料75份 、集骨材料15份和外添加复合材料a组分10份。
24.作为一种优选地实施方案,外添加复合材料b组分材料配置:以重量份计,称取早强速凝材料2份;表面活性材料2份;激发促进材料2份 和胶凝材料15份,将各组分拌合均化后,得到洗沙泥基免烧砖的外添加复合材料b组分原料;本发明一种洗沙泥基免烧砖(下文称为方案b),以重量份计,包括洗沙泥原料75份 、集骨材料15份和外添加复合材料b组份10份。
25.作为一种优选地实施方案:外添加复合材料c组分材料配置:以重量份计,称取早强速凝材料1份;表面活性材料1份;激发促进材料1.5份和胶凝材料15,将各组分拌合均化后,得到洗沙泥基免烧砖的外添加复合材料c组分原料;本发明一种洗沙泥基免烧砖(下文称为方案c),以重量份计,包括洗沙泥原料75份; 集骨材料15 份和外添加复合材料c组份10份。
26.作为一种优选地实施方案,外添加复合材料d组分材料配置:以重量份计,称取早强速凝材料1.5份;表面活性材料1.5份;激发促进材料1.5份和胶凝材料15,将各组分拌合均化后,得到洗沙泥基免烧砖的外添加复合材料d组分原料。
27.本发明一种洗沙泥基免烧砖(下文称为方案d),以重量份计,包括洗沙泥原料75份; 集骨材料15份和外添加复合材料d组份10份。
28.下面以实施b组分制备得到洗沙泥免烧制砖(即以方案b)为例。先做配比击实试验确定最佳含水率和最大干密实度,再通过静压设备成型洗沙泥砖,放于养生室自然养护7(6 1)天、28天后测量无侧限抗压强度。
29.按照方案a、b、c和d的产品配方制备洗沙泥免烧制砖产品养护好试样进行水稳定性测试,测试结果均为洗沙泥免烧砖常温下浸泡水不解散,水稳定性好,耐久性好。
30.按照方案a、b、c和d的产品配方制备洗沙泥免烧制砖产品养护好试样进行无限抗侧压强度测试,抗冻融循环测试,吸水率测试,软化系数测试等,试验结果如表1所示。其中,方案a、b、c和d的制砖方法采用相同的免烧砖的成型方法,工艺步骤与条件均相同。
31.表1 方案a、b、c和d的检测试验结果:
32.表1分析表1数据可见,观察试验过程试样品数据变化,本发明外添加复合原料组分配比合理,试样各项性能参数优异,无限侧抗压强度符合mu10~mu15标准,其方案a、b、c和d均符合国家行业标准要求。
33.采用上述方案后,本发明一种洗沙泥基免烧砖,可实现弃泥固废原料100%资源再生利用,产品质量强度达到国家行业标准(符合mu10~mu20标准),弃泥掺配量行业最高≥80%,耐水性即抗冻融性符合15次~25次循环检测,综合性价比行业内最优,终端产品可实现多元化,即一条生产线只需通过更换不同外形模具即可实现不同产品,即减少项目投入成本,以增加产品多品种多附值性价比(如标砖、仿古青砖、多孔砖等),同时弃泥免烧制生态环保砖不仅解决了土地占用问题,同时还解决生态环保问题。
34.实施例2一种洗沙泥基免烧砖的成型方法,制备过程中所用免烧砖的制砖系统包括:泥料来料预置系统,原料仓储计量系统,原料混合搅拌系统,原料水分陈化均化拌和系统,原料均化粉破系统,免烧静压成型制砖系统,自动砖坯码垛系统和产品养护系统。
35.作为一种优选地方案,所述泥料来料预置系统工艺,包括依次相衔接的自动喂设备,对辊破碎设备和粉破设备等装置,相应地,依次设计三道工序处理。将处理好的洗沙泥料(含水率8~15%,具体可为12%)输送至原料储料仓。所述自动喂料设备,其作用是将洗沙泥料进行均匀输送给料,让下道处置工序不会出现堵料现象。所述对辊破碎设备,其作用是将上道工序送来的洗沙泥料进行0.5~10mm对辊压制,将洗沙泥块或掺杂其中石块等物进行压破,避免大硬块物遗露损伤成型模具,同时让洗沙泥料更均化进入到下道工序。所述粉破设备 ,其作用是将上道工序送来的均等粒径洗沙泥料进行更充分的破碎,使其泥料颗粒直径均化在≤3mm占总量的80%; 在3~5mm占总量的15%;在5~8mm占总量的5%。破碎好的泥料将输送至下道设计系统工序。
36.作为一种优选地方案,所述原料仓储计量系统工艺,包括plc电控操作计量系统,计量储存仓,粉体储存罐,液体计量容器等设计。此道工序作用是将洗沙泥免烧制砖各所需原料按最佳配比方案进行plc电控设定计量操作。
37.所述plc电控操作计量系统,由设备程序设计员按洗沙泥免烧制砖生产线设计工艺进行操作指令编辑,在实操过程中,并按最佳配比方案进行各原料需求进行数据调整编辑。经确认操作指令,设备将全自动配比计量称重。
38.所述计量储存仓,按洗沙泥免烧砖所需原料进行储存仓数设计,一般储存仓容积设计为4~6方,设计个数为三个储存仓,设计三合一电子全自动感应称计量。设计电子感应称称量范围在0~2000kg。
39.所述粉体储存罐,其作用是盛装粉体物料,包括胶凝材料水泥,(除去水泥外的)其他外添加复合材料中的粉体试剂等,确保粉体原料操作全程无粉尘,污染环境。粉体储存罐设计个数一般为1~2个,其容积大小为100吨或50吨各一个。
40.所述液体计量容器,其作用是将盛装液体物料,包括水,外添加复合材料中的液体试剂等,由plc电控全自动计量与配置,设计液体容器大小1吨水容积,设计个数为2~3个。
41.作为一种优选地方案,所述原料混合搅拌系统工艺,包括强制式混合搅拌设备和加湿雾化双组交错喷头组件。此道工序作用是将各原料(按最佳配比plc电控设定计量)汇
集至强制式混合搅拌设备中进行各原材料拌和操作。先干料拌和1~2分钟,再加水喷雾拌和1分钟。干拌和原料效果为湿拌和原料效果的3~5倍。
42.所述强制式混合搅拌设备,其作用是将plc电控计量好的各原料汇集在一起进行首次原料混合搅拌。强制式混合搅拌设备容积大小选项由设备生产线产能决定。
43.所述加湿雾化双组交错喷头组件,其作用是将水和/或外添加复合材料中的液体试剂,通过高压泵输送加湿雾化双组交错喷头组件,再经雾化喷头进行液体均化喷洒至强制式混合搅拌原料上。其交错喷头组件是指将雾化喷头交错安装并呈45度角分布焊接在一条直线管道上,有直线管道可调节方位角度。确保强制式搅拌内部喷淋无死角。
44.作为一种优选地方案, 所述原料水分陈化均化拌和系统工艺,包括行星搅拌设备和补水加水系统。此道工序作用是将上道工序输送过来的加湿混合原料进行补加水和让水份在原料中更加均化,保持原料颗粒表水渗透。
45.所述行星搅拌设备,其作用是将上道工序加湿搅拌好的原材料进行二次拌和,使原料颗粒表水份渗透均化。行星搅拌设备容积大小按照生产线产能配置选型。
46.所述补水加水系统(雾化喷淋系统),其作用中根据各原料混合水份均化程度不同,或原料在行星搅拌设备中运行时间过长时,需通过补水加水系统进行添加水份,调湿混合原料湿度。
47.作为一种优选地实施方案,所述原料均化粉破系统工艺,包括双级无筛网粉破碎设备。此道工序作用是将上道工序拌和原料因加水搅拌成团,导致砖样产品各原材料含水不均,或原料传送有较大未破原料颗粒,需再次进行颗粒破碎,使之颗粒细化。
48.所述双级无筛网粉破碎设备,其作用是将上道工序输送来的成团原料进行再次破碎,使各原材料颗粒更好地与胶凝材料及其它外添加复合材料进行均化混合。
49.作为一种优选地实施方案,所述免烧静压成型制砖系统工艺,包括储料仓与传送系统,挤压成型系统。此道工序作是免烧制砖的核心,它解决了原材料再次均化,原料压缩填充高度,产品成型及强度等作用。
50.所述储料仓与传送系统,此系统包括上部储料仓和下部皮带输送,上部储料仓用作原料临时堆放,一般设计容积0.3~0.5立方;下部皮带输送,将储料仓内混合好的原料输送至挤压成型系统的布料车内。
51.所述挤压成型系统,其作用是先用布料车将混合原料进行模具填充布料,其次模具上压头组件由plc电控设定符合原料特性的各部参数,进行模具上压头下降压制,在上下压头挤压过程中,模框进行连到排气泄压,当模具上下压头行走至设定产品高度位,模具上压头上升,下压头在模框反向运行即向下运行时间将挤压制成型的产品顶出模框面,再收抱夹器将产品抱住送至产品皮带输送带上。
52.作为一种优选地方案,所述自动砖坯码垛系统工艺,包括皮带接收传送系统,残料或余料回收系统,自动砖坯码垛系统,自动托板输送系统。其作用是将挤压成型系统制作出的砖坯产品通过抱砖器输送至皮带接收传送装置,由plc精准定位传送至行车或机械臂码垛位置,再由行车或机械臂自动进行砖坯码垛。
53.所述皮带接收传送系统,其作用是将挤压成型好的砖坯,直线式输送至行车码垛位,此结构设计分上下两层:上层设计为皮带传送,下层设计为残料回收皮带传送。
54.所述残料或余料回收系统,其作用是将主机成型部位所产生的余料或破损不良品
进行自动回收利用。
55.所述自动砖坯码垛系统,其作用是将皮带输送过的砖坯转移至托板上进行自动堆垛,堆垛层数可选9~11层。
56.所述自动托板输送系统,其作用是将叠起好的托板,按plc电控进行进托板传送至行车码垛设定位置。行车码垛系统将堆垛好托板层数,托板传送系统自动向前移动一个托板位。
57.作为一种优选地实施方案,所述产品养护系统工艺,包括简易厂棚房,加湿雾化喷淋系统。其作用是将刚生产出的砖坯,送至自然养护区进行无洒水一周养护,然后产品打包转移户外堆场养护出售,养护温度常温即可;当外界环境过高达30~40度或以上时,需养护区保湿空间养护。
58.所述简易厂棚房,其作用是防止砖坯刚成型被光晒或被雨淋即防止暴晒暴淋,导致砖坯表面因高温失水份开裂,或淋雨砖坯脱皮掉渣。
59.所述加湿雾化喷淋系统,其作用是防止天气气温过高或风吹干燥砖坯,使用其表面因失水而开裂。
60.需要说明的是,本发明的制砖系统的组成部分,可根据实际所需进行自由组合使用。
61.本发明的所述免烧砖的制砖方法,如图1所示,包括如下步骤:步骤s1,泥料来料预置处理:使用泥料来料预置系统将含水率为8~15%(可通过添加干燥剂或晾干等方式得到)的洗沙泥料转移至喂料机进行均匀给料,然后将洗沙泥料输送至下道对辊机进行集骨材料破碎与泥料辊压变薄处理,对辊间距调整为0.5~10mm;对辊处理过的洗沙泥料用皮带输送至下道粉破机进行洗沙泥料的粉破与打散,粉破后的洗沙泥料中,颗粒细化至泥粒径≤3mm的部分占80%,以及3~8mm的部分占20%;步骤s2,原料仓储计量处理:使用原料仓储计量系统设定plc电控参数并控制储料仓各原料计量数与传送,其中,原料计量包括符合颗粒级配的洗沙泥料,其掺配比占75~80%;集骨材料,其掺配比占5~15%,集骨材料符合颗粒级配,颗粒径≤5mm的部分占80%,5~10mm的部分占15%,以及10~15mm的部分占5%;然后将步骤s1上道工序粉破机破碎好的洗沙泥料由皮带输送至储料仓存储,集骨材料由铲车从集骨材料堆场转移至储料仓;由plc电控操作皮带电子感应称进行洗沙泥料和集骨材料的分别计量;同时设定plc电控参数并控制各电子感应称进行各其他原料的分别计量并输送至原料混合搅拌系统,其中水的掺配量为2~8%、胶凝材料水泥的掺配量为8~15%,余下其他外添加复合材料的掺配量为0.05%,设定plc电控参数并控制各电子感应称进行计量并输送至下道工序原料混合搅拌系统;步骤s3,原料混合搅拌处理:使用原料混合搅拌系统将上道工序原料仓储计量系统计量得到的计量原料进行半干法混合搅拌,搅拌时间2~3min,转速25~35t/min;由于混合原料为半干湿状态,可减少扬尘与粉尘产生,同时原料混合搅拌系统采用节点收尘法,将对局部微小的粉尘点产生进行脉袋吸尘处理,即起到收尘除尘,又节省投资成本。
62.将各计量原料先在强制式混合搅拌机内进行粉体原料的混合搅拌,先将粉体原料干拌和,拌和时间2min,再用雾化喷淋加水湿法拌和,拌和时间1~1.5min,混合搅拌后得到
半干湿原料,接着将混合搅拌好的所述半干湿原料将输送至下道工序原料水分均化拌和系统。
63.所述原料混合搅拌系统设计雾化喷淋进行抑尘降噪处理;同时主控设备设计采用半沉降式安装法,易做封闭式管控与收尘处理,即起到美化效果,减少资金投入,又改善和提高了环保保护。
64.步骤s4,原料水分均化拌和处理:使用原料水分均化拌和将步骤s3混合的半干湿原料再次进行均化拌和搅拌,拌和时间2~3min,转速20~30t/min,让半干湿原料的颗粒表面在加水湿化后使水分子更加均匀地附着在泥颗粒表面并陈化渗透,再次拌和好的加湿混合原料将输送至下道工序原料均化粉破系统;步骤s5,原料均化粉破处理:使用原料均化粉破系统将步骤s4加湿均化混合原料进行破碎,再次确保各原材料无成团集块,使得原料的颗粒之间的接触面积更大,减少颗粒间隙,确保后继主机成型布料容重比一致性,同时让各原料打散均化,增强洗沙泥料的可塑性,减少泥料挤压成型砖坯后返弹开裂。破碎所用的原料粉破机运行转速120~140t/min,每小时处理破碎原料50~100t,其设备按生产线产能设计选型。混合原料粉破后将输送至下道工序免烧静压成型制砖系统;步骤s6,免烧静压成型制砖处理:使用免烧静压成型制砖系统将步骤s5均化粉破处理后的原料进行免烧砖坯挤压成型;挤压成型工艺流程的操作顺序依次为:混合原料储存、布料车搅拌与布料、上下挤头与模框素互锁联动完成砖坯成型、以及夹砖器抱送成型砖坯至输送皮带,再由其将成型砖坯送至下道工序。上述混合原料储存其作用确保主机挤压成型连续原料提供,同时让混合原料水份堆积渗透作用。上述布料车搅拌与布料其作用是首先有存储原料功能只少保证3~4次成型原料量存积;上述上下挤头与模框素互锁联动完成砖坯成型其作用是通过上压下顶模拟式双压挤压成型,同时与模具模框互锁联动结构设计来完成洗沙泥砖坯成型所达到的一系列功能参数,包括压制力度,成型高度,砖坯密实度,砖坯表面光洁度等。上述夹砖器抱砖功能其作用是将成型好的砖坯从模具位转移至皮带传送位。成品砖坯由皮带传送至下道自动砖坯码垛系统。
65.步骤s7,自动砖坯码垛处理:使用自动砖坯码垛系统将步骤s6皮带传送过来的成型砖坯进行砖板码垛堆放(一般设定码垛高度为9~11层)。自动砖坯码垛系统包括自动栈板输送机,行车或机器手自动码垛设备。上述自动栈板输送机包括了栈板叠垛装置,进栈板输送装置,红外线光感定位装置等其功能作用是将栈板进行进栈板,输送栈板,定位栈板,传送栈板等;上述行车或机器手自动码垛设备包括固定座,伸曲臂,抓取臂,收缩夹等其功能作用是从皮带输送过来的成品砖坯转移至栈板上,并进行9~11层高度均致码垛堆放。
66.步骤s8,产品养护处理:使用产品养护系统将步骤s7码垛后的成品砖坯进行养护期内无洒水自然养护,养护后得到的砖平均符合国家行业mu10~mu20标准,具有良好的抗折度、抗压度及耐水性。
67.作为一种优选地实施方式,步骤s6中,所述布料车内设三联机械搅拌结构设计,布料时,将混合原料布料于模具腔内,同时利用所述三联机械搅拌结构将混合原料进行再次拌和均化,并且在下料的同时形成挤压布料,即让混合原料进行均化布料于模具腔内,同时
形成挤压布料,还将混合原料进行再次拌和均化,并且确保每模腔原料容重比的一致性。
68.作为一种优选地实施方式,步骤s3中,所述原料混合搅拌系统包括强制式混合搅拌设备,以及用于喷洒水分或外添加液体试剂的加湿雾化双组交错喷头组件,所述加湿雾化双组交错喷头组件,所述加湿雾化双组交错喷头组件包括交错喷头,所述交错喷头交错安装并呈45度角分布焊接在一条直线管道上。确保强制式搅拌内部喷淋无死角。
69.喷洒时,交错喷头将液体均化喷洒至所述强制式混合搅拌设备的搅拌原料上。
70.作为一种优选地实施方式,步骤s8中,产品养护处理时,成品砖坯由叉车转移至简易厂棚养护区进行自然养护或养护窑恒温养护,砖坯养护方式与时间快慢取决于项目的土地与资金。上述简易厂棚养护,设计成阳光板房,其内增设加湿雾化喷淋装置,在气温达35~40度时可启用加湿空气养护。采用阳光板房结构,可以增加养护区内温度加快砖坯产品凝固速度,缩短砖坯养护周期(一般自砖坯成型自然养护3~5天,然后打包堆垛三层高,可节省场地面积,养护期间无需洒水养护,养护周期3周左右即可产品销售),厂棚阳光板房养护设计最大优势是投资小,节省成本。上述养护窑恒温养护结构设计,在恒温恒湿条件下养护砖坯产品(恒温在35~45度,相对湿度75~90%,连续1~2天养护),将缩短砖坯养护周期(产品养护周期1~2周即可产品销售)。上述恒温条件提供可采用热蒸气或电等加热方式提供热源,上述恒湿条件采用水气加湿设备提供湿度。
71.本发明采用阳光板房作养护区,达到了增温效果,收短产品养护周期,且整个产品养护期间无洒水养护,避免造污水二次污染风险和节约水源,降低运营成本。
72.本发明一种洗沙泥基免烧砖的成型方法,能将洗沙泥100%资源再生利用。经过本发明制砖系统成型,同时配合免烧砖的主材料及外添加复合剂,从而可保证洗沙泥免烧砖产品的高致密性,降低砖体毛细孔率,减少吸水率(≤15%),提高产品软化系数(≥0.8)和耐水性能(抗冻融测试10~25次),最大实现洗沙泥掺配量(≥80%),是一种低成本(0.18~0.25元/块),压实度致密,高强度(mu10~mu20),耐候性好的环保节能免烧泥砖。
73.需要说明的是,(1)本发明的产品组分配比可采用其他成型方法进行成型加工,以能实现相应的产品质量要求即可。本发明的成型方法也可采用其他产品组分配比进行加工,以能实现相应的产品质量要求即可。(2)本发明所用外添加复合材料均为行业内公知的材料,本发明所用的外添加复合材料为市场上购买所得。
74.上述实施例和附图并非限定本发明的产品形态和式样,任何所属技术领域的普通技术人员对其所做的适当变化或修饰,皆应视为不脱离本发明的专利范畴。