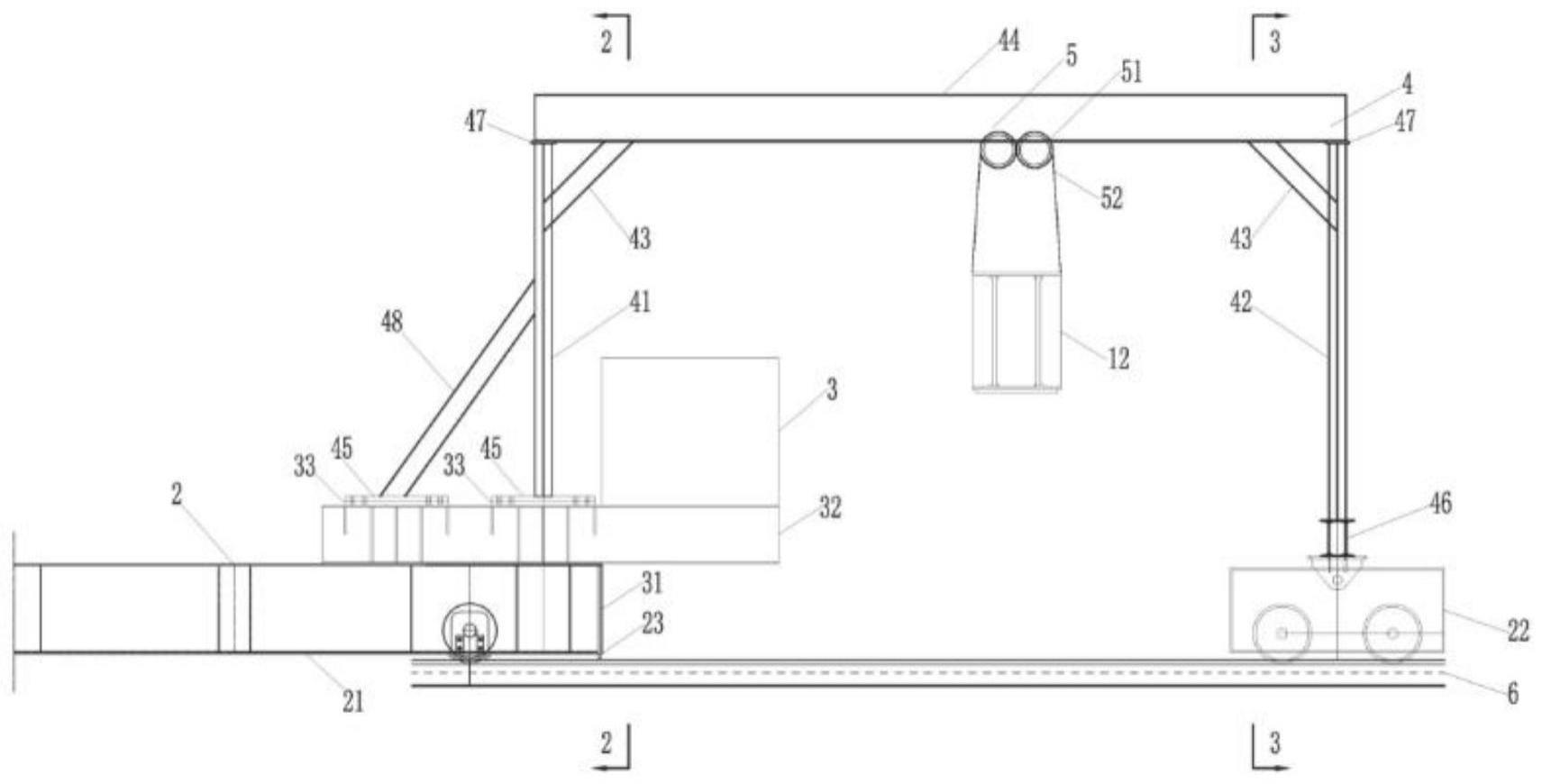
1.本发明涉及钢桁梁锚座技术领域,具体是涉及一种钢桁梁锚座装置安装系统。
背景技术:2.单点单向拖拉换梁施工涉及的锚固结构主要有反力座、锚梁、锚固牛腿及锚固滑块等。反力座的主要作用是为拖拉用千斤顶提供支撑,穿过穿心千斤顶的钢绞线与固定于旧钢桁梁上的锚梁、新钢箱梁上的锚固牛腿及锚固滑块相连实现拖拉功能;
3.拖拉换梁锚固结构中钢桁梁锚座装置主要包括反力座和锚梁,钢桁梁锚座装置的安装难度最大、风险最高,相关技术中,钢桁梁锚座装置的安装通常采用分离式走行吊架、折臂吊轨道平板车等,但是,分离式走行吊架在锚梁的运输及安装过程中存在偏载的情况,需采用水箱或沙袋进行配重和逐级卸载,折臂吊轨道平板车由于起重能力有限,锚梁需要分段制作现场拼装,因此,上述两种施工方式劳动强度大、施工效率低、安全风险高。
技术实现要素:4.本发明的目的是为了克服上述背景技术的不足,提供一种钢桁梁锚座装置安装系统。
5.本发明提供一种钢桁梁锚座装置安装系统,包括:安装系统包括锚座系统、走行系统、存放系统、门架系统、起吊系统,导向系统和拖拉系统,所述安装系统安装于钢桁梁上;
6.所述锚座系统设置于钢桁梁和存放系统上,所述存放系统的上方设有门架系统,所述门架系统和存放系统的下方均设置有走行系统,所述起吊系统设置于门架系统上,所述导向系统设置于走行系统的下方,所述拖拉系统设置于锚座系统上。
7.进一步地,所述门架系统包括工轨道梁、前支撑腿、后支撑腿、顶部钢板,所述前支撑腿和后支撑腿垂直设置于工轨道梁下端面的两侧,工轨道梁、前支撑腿和后支撑腿整体呈龙门架结构,顶部钢板设置于工轨道梁的下端面,且分布于前支撑腿和后支撑腿连接。
8.进一步地,所述门架系统还包括两个斜撑杆、槽斜撑,两个斜撑杆分别设置于工轨道梁与前支撑腿和后支撑腿的连接处,槽斜撑设置于前支撑腿的一侧。
9.进一步地,所述门架系统还包括底板法兰和双拼工型钢分配梁,所述底板法兰分别设置于前支撑腿和槽斜撑的下端面,所述双拼工型钢分配梁设置于后支撑腿的下端面。
10.进一步地,所述走行系统包括轨道平板车、走行轮箱和多个夹轨器,所述轨道平板车设置于前支撑腿下方,走行轮箱设置于双拼工型钢分配梁的下端面,多个夹轨器分别设置于轨道平板车和走行轮箱的下端面。
11.进一步地,所述存放系统包括:
12.平板车大纵梁,设置于轨道平板车的上端面;
13.双拼型钢纵梁,设置于平板车大纵梁的上端面;
14.定位法兰,设置于双拼型钢纵梁的上端面,且与底板法兰连接;
15.槽小横梁,均匀分布在双拼型钢纵梁悬挑端的顶面;
16.花纹钢板,设置于槽小横梁上;
17.加劲板,设置于双拼型钢纵梁的两侧,且上端面与定位法兰连接。
18.进一步地,所述起吊系统还包括电动葫芦和控制系统,所述电动葫芦设置于门架系统上,所述控制系统安装于电动葫芦的下端面。
19.进一步地,所述锚座系统设置于钢桁梁的一侧,锚座系统包括反力座和锚梁,所述反力座设置于钢桁梁的一侧,锚梁设置于反力座的一侧。
20.进一步地,所述导向系统包括第一轨道,所述第一轨道设置于走行系统的下方。
21.进一步地,所述拖拉系统包括:
22.支架滑道梁,设置于反力座的一侧;
23.墩顶滑道梁,设置于钢桁梁的墩顶上;
24.mge板,分别设置于支架滑道梁和墩顶滑道梁上;
25.拖拉千斤顶,设置于反力座上;
26.钢绞线,设置于拖拉千斤顶上,另外一端设置于锚座系统上。
27.与现有技术相比,本发明的优点如下:通过安装系统,实现在安全风险可控的情况下实现锚座装置的快速安装,解决传统钢桁梁锚座装置安装中存在劳动强度大、施工效率低、安全风险高的缺点。同时也提供了一种全新的钢桁梁锚座装置和安装系统,可以用于特大桥上部结构维修加固施工中,尤其是新钢箱梁替换旧钢桁梁的拖拉换梁施工中。
附图说明
28.图1是本发明整体正面剖视示意图。
29.图2是本发明存放系统侧视示意图。
30.图3是本发明走行系统侧视示意图。
31.图4是本发明锚座装置安装系统平面示意图。
32.图5是本发明钢桁梁拖拉系统立面示意图。
33.图6是本发明锚座系统侧视示意图。
34.图7是本发明钢桁梁锚座立面示意图。
35.图中:
36.1、锚座系统;11、反力座;12、锚梁;
37.2、走行系统;21、轨道平板车;22、走行轮箱;23、夹轨器;
38.3、存放系统;31、平板车大纵梁;32、双拼型钢纵梁;33、定位法兰;34、槽小横梁;35、花纹钢板;36、加劲板;
39.4、门架系统;41、前支撑腿;42、后支撑腿;43、斜撑杆;44、工轨道梁;45、底板法兰;46、双拼工型钢分配梁;47、顶部钢板;48、槽斜撑;
40.5、起吊系统;51、电动葫芦;52、控制系统;
41.6、第一轨道;7、钢桁梁。
42.8、拖拉系统;81、支架滑道梁;82、墩顶滑道梁;83、mge板;84、拖拉千斤顶;85、钢绞线。
具体实施方式
43.现在将详细参照本发明的具体实施例,在附图中例示了本发明的例子。尽管将结合具体实施例描述本发明,但将理解,不是想要将本发明限于所述的实施例。相反,想要覆盖由所附权利要求限定的在本发明的精神和范围内包括的变更、修改和等价物。应注意,这里描述的方法步骤都可以由任何功能块或功能布置来实现,且任何功能块或功能布置可被实现为物理实体或逻辑实体、或者两者的组合。
44.为了使本领域技术人员更好地理解本发明,下面结合附图和具体实施方式对本发明作进一步详细说明。
45.注意:接下来要介绍的示例仅是一个具体的例子,而不作为限制本发明的实施例必须为如下具体的步骤、数值、条件、数据、顺序等等。本领域技术人员可以通过阅读本说明书来运用本发明的构思来构造本说明书中未提到的更多实施例。
46.拖拉换梁锚固结构中钢桁梁锚座装置主要包括反力座和锚梁,钢桁梁锚座装置的安装难度最大、风险最高,相关技术中,钢桁梁锚座装置的安装通常采用分离式走行吊架、折臂吊轨道平板车等,但是,分离式走行吊架在锚梁的运输及安装过程中存在偏载的情况,需采用水箱或沙袋进行配重和逐级卸载,折臂吊轨道平板车由于起重能力有限,锚梁需要分段制作现场拼装,因此,上述两种施工方式劳动强度大、施工效率低、安全风险高。
47.为了解决上述钢桁梁存在的问题,本发明提出的一种钢桁梁锚座装置安装系统,参见图1,本技术中,包括:安装系统包括锚座系统1、走行系统2、存放系统3、门架系统4、起吊系统5,导向系统和拖拉系统8,安装系统安装于钢桁梁7上;锚座系统1设置于钢桁梁7和存放系统3上,存放系统3的上方设有门架系统4,门架系统4和存放系统3的下方均设置有走行系统2,起吊系统5设置于门架系统4上,导向系统设置于走行系统2的下方,拖拉系统8设置于锚座系统1上,
48.本实施例中,将反力座11待安装位置处钢桁梁7竖杆和锚梁12待安装位置处上平联相应构件拆除,保证反力座11安装空间和锚梁12的顺利下放,在反力座11安装位置提前进行反力座11安装,安装前将钢桁梁7下弦杆顶面相应位置处油漆打磨干净,借助轨道平板车21将反力座11各构件运至指定位置,按要求顺序完成反力座11安装,反力座11安装完成后,进行钢桁梁7锚梁12的安装,将轨道平板车21、走行轮箱22、前后支撑腿42、轨道梁等进行现场组装,将组装后的钢桁梁7锚座系统1安装系统走行至锚梁12存放场地上方,对夹轨器23进行锁紧,利用汽车吊机将两组锚梁12依次吊运至安装系统锚梁12存放平台上。解锁夹轨器23走行至第一组待安装锚梁12上方,下放夹轨器23锁紧,移动电动葫芦51至锚梁12存放平台上方,下放吊钩通过吊带与锚梁12吊紧,缓慢向上提升锚梁12,离平台5cm左右后停止提升,进行观察,待锚梁12稳定、结构系统无异常后进行横移,缓慢横移至锚梁12待安装位置上方后停止,观察无异常后,从上平联缺口处缓慢下放,利用倒链人工配合进行下放,保证下放过程平稳、安全。调整好位置后,进行锚梁12就位、固定,完成第一组钢桁梁7锚梁12的安装,解锁夹轨器23走行至第二组待安装锚梁12上方,下放夹轨器23锁紧。重复上述步骤完成第二组钢桁梁7锚梁12安装,依次完成剩余钢桁梁7锚梁12安装。
49.在上述实施例的基础上,本实施例中,门架系统4包括工轨道梁44、前支撑腿41、后支撑腿42、顶部钢板47,前支撑腿41和后支撑腿42垂直设置于工轨道梁44下端面的两侧,工轨道梁44、前支撑腿41和后支撑腿42整体呈龙门架结构,顶部钢板47设置于工轨道梁44的
下端面,且分布于前支撑腿41和后支撑腿42连接,门架系统4还包括两个斜撑杆43、槽斜撑48,两个斜撑杆43分别设置于工轨道梁44与前支撑腿41和后支撑腿42的连接处,槽斜撑48设置于前支撑腿41的一侧,门架系统4还包括底板法兰45和双拼工型钢分配梁46,底板法兰45分别设置于前支撑腿41和槽斜撑48的下端面,双拼工型钢分配梁46设置于后支撑腿42的下端面。
50.本实施例中,前支撑腿41下焊接底板法兰45,与定位法兰33通过螺栓连接固定于轨道平板车21的双拼型钢纵梁32上;后支撑腿42焊接固定于双拼工型钢分配梁46上,与走行轮箱22通过u型螺栓连接;前后支撑腿42通过法兰或u型螺栓与走行系统2连接,可以实现该系统的快速安拆和功能转换。前后支撑腿42顶部焊接顶部钢板47,顶部钢板47上设置工轨道梁44形成门架系统4,前支撑腿41与轨道平板车21间设置槽斜撑48,前后支撑腿42与工轨道梁44间设置斜撑杆43,从而保证门架结构的整体稳定。
51.参见图3,在上述实施例的基础上,本实施例中,走行系统2包括轨道平板车21、走行轮箱22和多个夹轨器23,轨道平板车21设置于前支撑腿41下方,走行轮箱22设置于双拼工型钢分配梁46的下端面,多个夹轨器23分别设置于轨道平板车21和走行轮箱22的下端面。
52.本实施例中,轨道平板车21自带折臂吊和发电机,提供动力,合理布置发电机和锚梁12存放区,避免位置冲突,走行轮箱22底部设有走行轮,安装于梁顶轨道结构上,门架系统4后支撑腿42底部与走行轮箱22采用u型螺栓连接,方便安装拆卸,轨道平板车21和走行轮箱22均设有夹轨器23,在起吊工况或静止状态下与第一轨道6锁紧。
53.参见图2、图4,在上述实施例的基础上,本实施例中,存放系统3包括:平板车大纵梁31,设置于轨道平板车21的上端面;双拼型钢纵梁32,设置于平板车大纵梁31的上端面;定位法兰33,设置于双拼型钢纵梁32的上端面,且与底板法兰45连接;槽小横梁34,均匀分布在双拼型钢纵梁32悬挑端的顶面;花纹钢板35,设置于槽小横梁34上;加劲板36,设置于双拼型钢纵梁32的两侧,且上端面与定位法兰33连接。
54.本实施例中,双拼型钢纵梁32与平板车大纵梁31采取焊接,焊缝高度hf=10mm,间距为50mm/150mm,双拼型钢纵梁32的悬挑长度为,在其悬挑端顶面均匀分布槽小横梁34,上面满铺花纹钢板35,空间大小满足2组钢锚梁12的存放要求,在其非悬挑端顶面设置定位法兰33,定位法兰3333与型钢纵梁采取焊接,与前支撑腿41和槽斜撑48的底板法兰45通过螺栓连接,方面安装拆卸。
55.在上述实施例的基础上,本实施例中,起吊系统5还包括电动葫芦51和控制系统52,电动葫芦51设置于门架系统4上,控制系统52安装于电动葫芦51的下端面。
56.本实施例中,电动葫芦51安装于轨道梁上,采用电动葫芦51用于起吊钢桁梁7锚梁12,用于新钢箱梁替换旧钢桁梁7的拖拉换梁施工中,该拖拉系统8可以实现钢梁快速更换、施工效率高、成本较低。
57.参见图6和图7,在上述实施例的基础上,本实施例中,锚座系统1设置于钢桁梁7的一侧,锚座系统1包括反力座11和锚梁12,反力座11设置于钢桁梁7的一侧,锚梁12设置于反力座11的一侧,
58.本实施例中,反力座11位于钢桁梁7下弦杆顶面上,与下弦杆采取焊接,焊前需将该位置处油漆涂装打磨干净,焊缝采用熔透坡口焊,质量等级为二级;锚梁12主要由限位
板、加劲板36、垫板等构件组成,各构件间采用坡口焊缝或焊高hf=10mm双面角焊缝连接,若存在无法施焊位置则需磨光顶紧;反力座11和锚梁12的各构件采取工厂冷切割下料,锚梁12上构件的半圆形开孔需根据钢绞线85锚头大小确定,保证开孔精度,反力座11现场进行拼装焊接,焊前需拆除影响安装的钢桁梁7竖杆,锚梁12在厂内整体加工制作,利用锚座系统1安装系统吊运至现场后整体安装,吊运前需拆除影响安装的钢桁梁7上平联相应构件,可以实现锚座装置的快速安装,降低安装劳动强度和安全风险,提高安装施工效率。
59.在上述实施例的基础上,本实施例中,导向系统包括第一轨道6,第一轨道6设置于走行系统2的下方。
60.本实施例中,走行轮箱22底部设有走行轮,安装于梁顶第一轨道6结构上,便于整体装置进行移动。
61.参见图5,在上述实施例的基础上,本实施例中,拖拉系统8包括:支架滑道梁81,设置于反力座11的一侧;墩顶滑道梁82,设置于钢桁梁7的墩顶上;mge板83,分别设置于支架滑道梁81和墩顶滑道梁82上;拖拉千斤顶84,设置于反力座11上;钢绞线85,设置于拖拉千斤顶84上,另外一端设置于锚座系统1上。
62.本实施例中,在拖拉反力支架上布置支架滑道梁81,在各墩墩顶布置墩顶滑道梁82,在支架滑道梁81和墩顶滑道梁82上布置mge板83,以降低摩擦系数、提高拖拉效率,在拖拉反力座11后面布置两台350t拖拉连续拖拉千斤顶84,将钢绞线85一端顺序穿入拖拉千斤顶84内,另一端对应穿入钢桁梁7锚座系统1的锚梁12内。
63.在本发明的描述中,需要说明的是,术语“上”、“下”等指示的方位或位置关系为基于附图所示的方位或位置关系,仅是为了便于描述本发明和简化描述,而不是指示或暗示所指的装置或元件必须具有特定的方位、以特定的方位构造和操作,因此不能理解为对本发明的限制。除非另有明确的规定和限定,术语“安装”、“相连”、“连接”应做广义理解,例如,可以是固定连接,也可以是可拆卸连接,或一体地连接;可以是机械连接,也可以是电连接;可以是直接相连,也可以通过中间媒介间接相连,可以是两个元件内部的连通。对于本领域的普通技术人员而言,可以根据具体情况理解上述术语在本发明中的具体含义。
64.需要说明的是,在本发明中,诸如“第一”和“第二”等之类的关系术语仅仅用来将一个实体或者操作与另一个实体或操作区分开来,而不一定要求或者暗示这些实体或操作之间存在任何这种实际的关系或者顺序。而且,术语“包括”、“包含”或者其任何其他变体意在涵盖非排他性的包含,从而使得包括一系列要素的过程、方法、物品或者设备不仅包括那些要素,而且还包括没有明确列出的其他要素,或者是还包括为这种过程、方法、物品或者设备所固有的要素。在没有更多限制的情况下,由语句“包括一个
……”
限定的要素,并不排除在包括所述要素的过程、方法、物品或者设备中还存在另外的相同要素。
65.以上所述仅是本发明的具体实施方式,使本领域技术人员能够理解或实现本发明。对这些实施例的多种修改对本领域的技术人员来说将是显而易见的,本文中所定义的一般原理可以在不脱离本发明的精神或范围的情况下,在其它实施例中实现。因此,本发明将不会被限制于本文所示的这些实施例,而是要符合与本文所发明的原理和新颖特点相一致的最宽的范围。