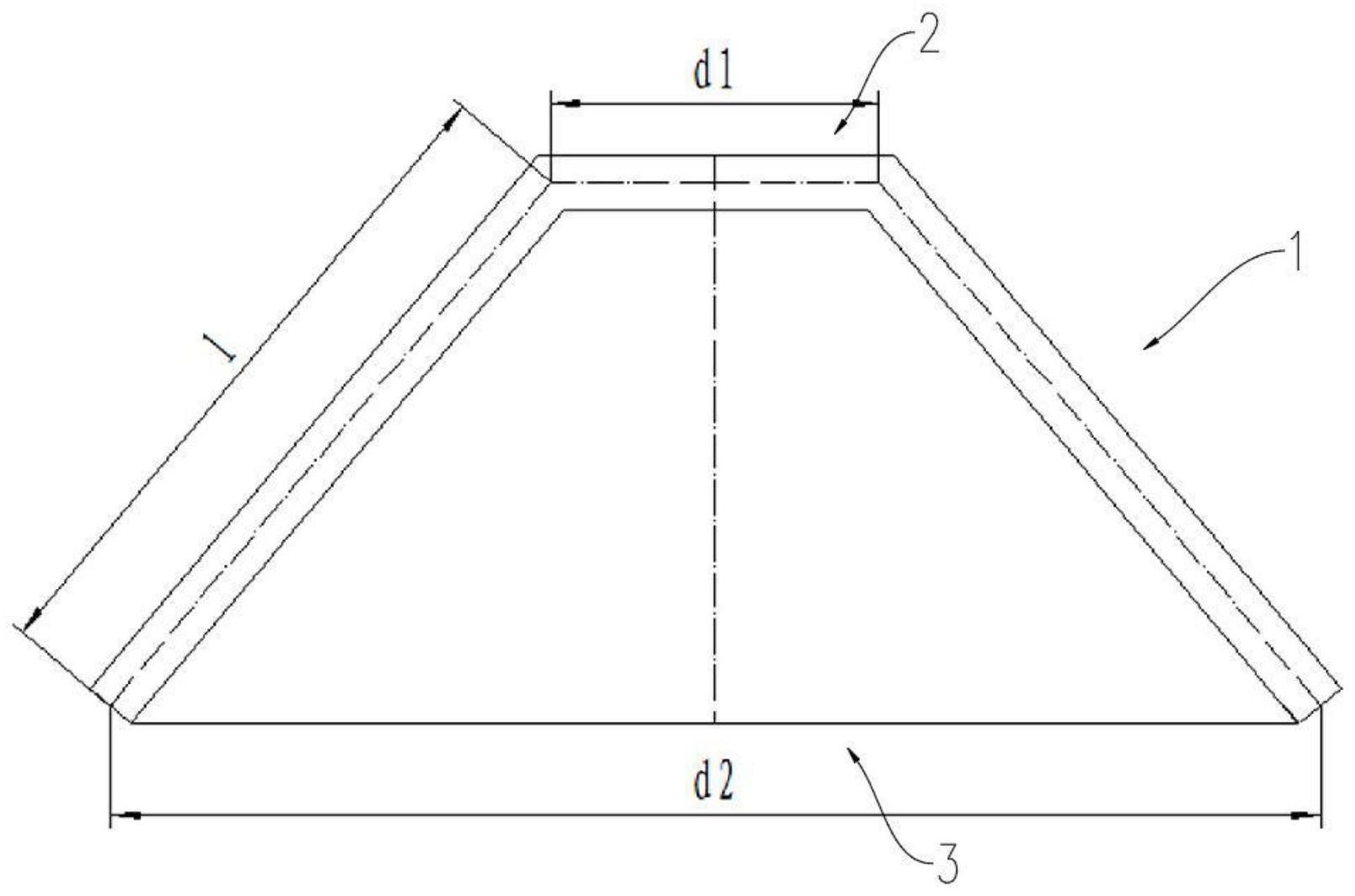
1.本发明涉及拉深成形技术领域,具体是指一种碟式离心机分配器下体热拉深成型方法。
背景技术:2.拉深成形是通过模具对板料施加复杂的外力,引发板内出现复杂的应力状态,促使板料产生理想方向的流动。在拉深成形过程中,需要安装压边装置产生摩擦抗力,以增加板料中的拉应力,控制材料的流动,避免起皱。压边力的大小是板材拉深成形中的重要工艺参数和控制手段。传统的板材拉深成形方式往往通过单动压力机的弹性压边圈和双动压力机的固定压边圈来产生拉深成形所需的压边力。
3.生产过程中经常会遇到一些类似锥形件但结构复杂的旋转体,常规的毛坯成形方法可以通过锻造、铸造、板料卷焊以及旋压等方式获得,但是对于壁厚在15~25mm范围内的工件采用锻件或原材料生产,材料利用率仅有8%~10%,机加工作量大,效率低,零件的制造周期和成本较高;采用整体铸件因为不锈钢流动性差,铸造缺陷明显,常有砂眼、缩孔、裂纹,废品率高;采用板料卷焊材料利用率虽然大幅提高,但焊接变形严重,工序繁多,工效、可靠性和合格率都较低;采用旋压对毛坯的厚度有一定的限制,在旋压初期还会产生严重的加工硬化需通过退火处理才能继续成形。分配器下体就属于该类锥形件。
4.鉴于以上,有必要提出一种碟式离心机分配器下体热拉深成型方法来解决上述问题。
技术实现要素:5.本发明的目的是为了解决上述技术问题,而提供一种碟式离心机分配器下体热拉深成型方法。
6.为了实现上述目的,本发明采用了如下技术方案:一种碟式离心机分配器下体热拉深成型方法,包括以下步骤:
7.(a)将分配器下体板料转化为形状简单的能够完全包容原零件的锥形件;
8.(b)零件成型性分析;通过一组算法,确定包容分配器下体原零件的锥形件是否满足拉深成型,如不满足拉深成型,则需要调整包容锥形件结构,直至满足要求为止,并根据锥形件尺寸来确定板料尺寸;
9.(c)热拉深成型;将板料预加热升温,然后置入拉深模中,利用电液锤的压力拉深成形。
10.进一步的,所述步骤(a)中,分配器下体转化为形状简单的能够完全包容原零件的锥形件,所述锥形件呈圆台形,锥形件小端直径为d1,锥形件大端直径为d2,锥形件高度为l。
11.进一步的,步骤(b)中,所述通过一组算法包括以下步骤:
12.锥形件的拉深过程,针对预成型工件的几何参数,即相对高度、锥度及材料的相对厚度不同,进行如下判断:
13.(1)拉深成型方法:
14.t/d
×
100》2.5时,此时材料的稳定性好,采用无压边的拉深模一次拉出;
15.t/d
×
100=1.5~2时,采用压边装置的模具一次拉出;
16.t/d
×
100《1.5或有较宽的凸缘时,采用压边装置,经多次拉深而成;
17.(2)毛坯直径的确定:
18.根据包容的锥形件,计算板料直径
19.其中d1是锥形件小端直径mm;d2是锥形件大端直径mm;是锥形件高度mm。
20.(3)锥形件拉深力公式f拉深=πd1tσbk
21.其中d1—小端直径mm;t—料厚mm;σb—材料的拉深强度:k—形状系数。
22.进一步的,所述锥形件采用06cr19ni10不锈钢材质。
23.进一步的,所述步骤c中为满足热拉深成型需要,同时保证不锈钢耐蚀性,将板料加热到1050~1150℃。
24.进一步的,,选择适合厚度的钢板做坯料,使拉深成型的壁厚在0.75t-1.2t。
25.与现有技术相比,本发明的有益效果是:碟式离心机分配器下体零件一般由不锈钢材料制造而成。针对06cr19ni10不锈钢材质冷成形回弹大、贴模性差的特点,申请人研究了采用热成形的方法保证了该零件的尺寸精度,同时分析了热成形中成形方法、成形温度、压边间隙、冲压压力等工艺参数对成形零件尺寸的影响,热成形工艺方式成形零件尺寸精准、成形效果好,适合高精度加工生产;并且拉深成形后只要作少量的机械加工,即可做出合格零件,生产周期缩短,零件几何精度高,强度好,生产成本降低,产品质量和工作效率显著提高。
附图说明
26.图1为碟式离心机分配器下体零件的结构示意图;
27.图2为本技术根据零件转化而来的拉深成形后的锥形件;
28.图3为本技术中根据图2简化后的几何图形;
29.图4为拉深成形模具的结构示意图;
30.图5为锥形件拉深成型后模拟回弹结构示意图;
31.图中:1、锥形件;2、小端直径;3、大端直径;4、凸模;5、凹模;6、压边装置。
具体实施方式
32.下面将结合本发明的实施例,对本发明的技术方案进行清楚、完整地描述,显然,所描述的实施例仅仅是本发明一部分实施例,而不是全部的实施例。
33.一种碟式离心机分配器下体热拉深成型方法,碟式离心机分配器下体其多为不锈钢材质加工成型,如图1所示,其为圆台形薄壁零件,根据零件加工精度要求,成型后零件的厚度减薄量需要控制在15%以内,同时需要保证零件的轮廓度公差在0.1mm以内,零件成型后的高度在
±
0.05mm的范围内。
34.通过对零件尺寸以及所用料进行分析,该零件的成形特点主要如下。
35.1)零件终成形的高度h公差为
±
0.05mm,轮廓度为0.1mm,直径公差为
±
0.1mm,要
保证零件型面贴合度和尺寸稳定均匀性,宜采用拉深成形,但应考虑在零件顶端区域内的减薄量,如果减薄较大,减薄量容易超差,更有甚者使顶部破裂。
36.2)材料采用06cr19ni10化不锈钢材料进行零件成形,由于材料的强度较高,塑性差,伸长率低,回弹大。零件成形时容易破裂,成形后产生的回弹会严重影响零件弧面轮廓以及零件的高度,不利于尺寸精度的控制。
37.锥形零件的拉深,一般可一次拉成,其拉深方法根据相对料厚t/d的不同,可选用带校正作用的凹模5、带压边圈的拉胀模、具有拉胀筋的凹模5或反拉胀凹模5等,但是根据相对料厚的不同,对于成型较难时,材料的塑性差、强度大、回弹大的特性,一次成形精度差,尺寸稳定均匀性没办法保证,成形高度较高,很容易顶部破裂,故采用多步成形的工艺,即第一道次以储料为主的拉深预成形和第二道次精成型工艺;在第一道次和第二道次之间进行零件的应力释放、升温提高可塑性等操作来保障零件成型的精度。
38.对于分配器下体零件加工时,为了提高板料对于模具的贴模性将分配器下体板的料转预先化为形状简单的能够完全包容原零件的锥形件1如图2所示,将结构复杂的零件转化为形状简单的能够完全包容原零件的锥形件1;所述锥形件1采用06cr19ni10不锈钢材质。
39.具体的,分配器下体转化为形状简单的能够完全包容原零件的锥形件1,所述锥形件1呈圆台形,锥形件1小端直径2为d1,锥形件1大端直径3为d2,锥形件1高度为l。
40.对于锥形件1进行拉深时,需要对零件进行成型性分析;具体的,通过一组算法,确定包容分配器下体原零件的锥形件1是否满足拉深成型,如不满足拉深成型,则需要调整包容锥形件1结构,直至满足要求为止,并根据锥形件1尺寸来确定板料尺寸;
41.具体的,如图3所示,锥形件1的拉深过程,针对预成型工件的几何参数,即相对高度、锥度及材料的相对厚度不同,确定毛坯的直径、拉深次数和需要的拉深力;具体进行如下判断:
42.(1)拉深成型方法:
43.t/d
×
100》2.5时,此时材料的稳定性好,采用无压边的拉深模一次拉出;
44.t/d
×
100=1.5~2时,采用压边装置6的模具一次拉出;
45.t/d
×
100《1.5或有较宽的凸缘时,采用压边装置6,经多次拉深而成;
46.(2)毛坯直径的确定:
47.根据包容的锥形件1,计算板料直径
48.其中d1是锥形件1小端直径2mm;d2是锥形件1大端直径3mm;是锥形件1高度mm。
49.(3)锥形件1拉深力公式f拉深=πd1tσbk
50.其中d1—小端直径2mm;t—料厚mm;σb—材料的拉深强度:k—形状系数。
51.拉深方法根据相对料厚t/d的不同,确定毛坯的直径、拉深次数和需要的拉深力。
52.加工对象为上部小端直径2为d1,下部大端直径3为d2,的圆台形零件,在拉深成形时如发生起皱缺陷,可用于反映球底类薄壁件拉深成形过程中的起皱规律。为了保证零件的几何精度,拉深成形后内外锥面需要精车加工,因此要留出足够的加工余量,同时考虑到拉深过程中的各处变形不均匀,壁厚在1.2t至0.75t变化,选择适合厚度的钢板做坯料。
53.根据上述方法计算拉深的可能性。当不能满足拉深的条件时,适当的调整简化后
锥形件1各部位尺寸,比例要恰当,圆角半径尽量大些,以利于成形和减少拉深次数,使其满足拉深工艺要求。
54.图4为拉深模具结构及尺寸示意图。拉深试件以凸模4定型,凸凹模5间隙为1.1倍板料壁厚、凹模5圆角半径为10mm。在根据上述拉深方法选择时,需要使用拉延筋时,拉延筋可设计为半圆形环筋,压边圈上设置凸筋,凹模5上设置凹槽,两侧设置过渡圆角、与凸筋匹配间隙为1.2mm。压边力和拉延筋对起皱的影响,在零件的拉深预成形过程中,压边力是影响成形的主要因素之一。当压边圈所给压力过小时,拉深件的法兰边与零件的侧面都有可能发生起皱现象;当压边圈所给压力过大时,零件的厚度减薄量容易超差,甚至发生拉断破裂的现象。
55.工件的顶部应变较大,符合零件拉深成形的特性,顶部为等双拉胀形区域,在凸模4摩擦力以及材料硬化的作用下,顶部减薄明显,故调整不同压边力和毛坯直径,也可以适当增加凸模4的小端圆角半径,或者适当增加凸凹模5间隙来进行调整。
56.对于t/d
×
100《1.5或有较宽的凸缘时,需加入采用压边装置6,并进行多次拉深操作,来避免零件边缘起皱以及破裂的情况,多次拉深可以使零件的贴模情况良好,使零件的厚度变化均处于公差允许范围之内,最大减薄处均位于零件顶端的小直径端,成型效果良好。
57.针对于零件拉深后的回弹,如图5所示,图中虚线箭头所示为零件的回弹力大小与回弹方向的示意图,零件成形后最大减薄处与最大回弹量处均位于零件的小直径顶端面;毛坯直径对减薄量及回弹的影响趋势是一致的。毛坯直径的变化对厚度的减薄量基本没有影响,而对零件顶部的最大回弹量却存在影响。
58.当毛坯直径增大时,零件成形后的最大回弹量变小,且在相同毛坯直径的拉深条件下,06cr19ni10材料的最大回弹量较大,因此,在零件的拉深控制试验中,多次拉深成型,也可有效应对零件成型后的回弹。
59.实际加工时,为了提高材料的可塑性,以及减少零件拉深过程中的形变以及褶皱,加工时,本实施例采用热拉深成型;将板料预加热升温,然后置入拉深模中,利用电液锤的压力拉深成形。为满足热拉深成型需要,同时保证不锈钢耐蚀性,将板料加热到1050~1150摄氏度。06cr19ni10材料的熔点在1398~1454摄氏度;本实施例将板料预先升温至靠近熔点的温度,从而大大提高了材料的可塑性,从而在拉深成型过程中可以进行较高精度的拉深塑形。
60.以上所述,仅为本发明较佳的具体实施方式,但本发明的保护范围并不局限于此,任何熟悉本技术领域的技术人员在本发明揭露的技术范围内,根据本发明的技术方案及其发明构思加以等同替换或改变,都应涵盖在本发明的保护范围之内。